第五章 CFB锅炉主要性能参数及结构尺寸的计算及选择
113
第五章
CFB锅炉主要性能参数及结构尺寸的计算及选择 5.1 5.1.1
如前所述,循环流化床锅炉燃烧室中上部为快速床。固体物料在一定气速条件下流化,当
气速低于Uc时,固体循环量对床层空隙率无明显影响;气速一旦超过
Uc,床层空隙率主要取
决于固体循环量。因此,对任一颗粒物料,当U=Uc时,床层达到饱和携带能力,物料便被大
量吹出,此时必须补充等同于携带能力的物料量才能使床层进入快速流态化状态。故Uc为该物料进入快速流态化时的操作气速,即初始快速流态化速度。在初始快速流态化Uc时的最小
加料率定义为最小循环量Rmin。
初始快速流态化速度Uc主要与物料特性有关,按照实验统计
Uc=(3.5~4.0)
Ut (5-1) 最小循环量可由以下经验关联式给出 6270
fpp
1.627
f
2.25
c
min)]
([g1640
ρ.ρ
ρd.
U
R
(5-2)
超过最小循环量后,在相同气速下,对应不同的循环量可以有不同的快速床状态。也可以
用不同的床存量对应的不同物料沿床高浓度分布表示不同的快速床状态。如图5-1所示。
5-1
第五章 CFB锅炉主要性能参数及结构尺寸的计算及选择
114
输送点速度
Ut是快速流态化操作的极限速度,此时床层空隙率纵向分布曲线的拐点恰好
位于布风板处,上部呈稀相气力输送状态。而燃煤循环流化床中,始终有部分粗颗粒存在,因
此床内是由鼓泡床与快速床叠和而成。上述所论述的状态转换是针对床上部的细颗粒而言。循
环流化床是能形成流态化的一种装置,它由带有布风板的提升管、分离器和分离物料回送装置
构成的。提升管内的流化状态则因固体物料的性质及流化风速的不同而不同。它的流化状态可
以是鼓泡床、湍动床、快速床以致气力输送态。
人们公认循环流化床锅炉需要一个大的循环物料流,以维持燃烧室内沿高度方向物料空间
浓度从下向上逐渐变化,而不能象鼓泡流化床锅炉那样密相区以上物料空间浓度迅速减少。仅
当沿床高度方向物料浓度逐渐减小并维持一定数值时,才有可能产生高度方向上的较强回混,
从而把燃料释放出的热量纵向传递并横向传给受热面。研究证明,随着循环量的增加,燃烧室
内物料的平均粒度明显降低,从而使密相区气体的分配中气泡相的比例增大,气相与乳化相传
质减弱,相应抑制了密相区的热量释放份额。再加上高度方向上物料回混的加强,才能使循环
流化床锅炉在密相段不设置受热面的条件下亦能达到热量平衡。清华大学的热态试验表明,在
通常循环流化床5m/s的热态气速下,循环流化床锅炉燃烧室内单位标态烟气携带的固体颗粒
量若小于0.7kg/Nm3,则锅炉整体显示出鼓泡床的燃烧特点;若超过
1kg/Nm3,稀相段平均空
隙率已达到0.98,呈现出与鼓泡床的不同的燃烧特点。
5.1.2
因此,循环流化床燃烧室内是由多重粒子构成的下部鼓泡床、上部快速床的复合流态。而
快速床的物料循环量可以在一定范围内变化。因此以物料循环量或物料浓度空间分布状态受到
烟速、煤种、煤粒度、分离器效率等不确定因素的影响。但无论如何变化,设计的基本条件是
一个假定的确定的状态,即在满负荷条件下的燃烧室物料浓度分布是确定量,相应传热系数沿
床高的分布也是确定的。这就是所谓的定态设计原则。能采取定态设计的基本理论根据在于,
循环流化床内有一个人为可调量-即床存量,可以在循环量或物料浓度发生漂移时通过调整床
存量而把流化状态调整回到设计态。定态设计是循环流化床锅炉燃料适应性的基础。
决定流态的关键参数是燃烧室截面烟气速度和燃烧室上部单位截面的物料携带率,它取决
于系统物料平衡能力和床存量。床存量是可调参数,它由操作者控制,在确定烟速下,由于其
它扰动影响了物料浓度分布偏离设计值时,可以恢复到设计状态。烟速是设计值,选择烟速最
低不能小于该平均粒度物料进入快速流态化时的操作气速,即初始快速流态化速度Uc。设计
者为追求较大的燃烧室截面热负荷,当然愿意提高操作速度,但是该值受到燃烧室受热面磨损
程度的限制。早期研发循环流化床时,曾经选择9m/s的流化速度,但是由于磨损,不能在燃
烧室有任何暴露的金属面受热面。后期各个公司以燃烧室沿气体流向的垂直受热面不磨损为界
限,把烟速逐步统一到4~6m/s的范围,也有个别特例,如CPC、circufluid。图5-2给出了定
态图谱以及国内外不同典型设计的锅炉产品(A~I)在其中的位置。随着技术的发展,这些产品
的状态也在不断优化。 第五章 CFB锅炉主要性能参数及结构尺寸的计算及选择
115
炉膛流化速度
uf m/s 0
1
2 3 4 5 6 7 8 9 5
-低硬度煤磨损限
C
D
E
G
H
I
B
A
清华推荐
F 循环流率
GS kg/(m2s) 10
30
5
10
15
20
25 6
-高硬度煤磨损限
4-流动要求的下限
2-高分离效率/低磨耗
3-一般分离效率/一般磨耗
1-极高分离效率/极低磨耗 5-2
在定态图谱中,曲线4代表循环流化床燃烧中,流动需要达到的下限,低于此下限,燃烧
行为和传热效果区域鼓泡床;曲线3代表床料粒度为200m时,不同流化风速下的实际可以
达到的循环量,应该高于设计选定的最大循环量,否则燃烧室稀相区无法达到快速床状态,设
计的锅炉的燃烧、传热无法实现。2和1两条曲线分别代表配备一级分离装置和二级分离装置
的循环流化床在特定风速下所能达到的最大循环量。曲线5和6分别代表燃用硬煤和褐煤的磨
耗极限,两条曲线是在投运锅炉上观察得到的。因此,设计中选定的状态是有限制的,主要是
燃烧传热等基本性能的要求以及磨损的限制。
流态确定后应当对循环系统进行物料平衡的校验,按照平衡理论校验系统分离器效率,在
给定煤种的成灰特性下是否可以使床质量达到要求,相应状态下的物料循环量(或用烟气所携
带的物料量表示)是否达到指定的状态。如果床质量或循环量达不到定态的要求,要么改进分
离器,要么提供辅助惰性床料,否则必须选择更低的状态。在物料系统平衡的计算中,应该考
虑脱硫石灰石在炉内的爆裂磨耗特性及反应活性对物料平衡的影响。
5.1.3
认识燃煤循环流化床的流动形态,必须理解它与化工反应器有所不同。对化工反应器,其
固体物料是相对稳定、筛分较窄的催化剂,分离器对该催化剂的分离效率很高。反应器对于固
体物料而言是一个闭口体系,仅对气体是开口体系。而燃煤循环流化床中煤中的灰份及脱硫用
的石灰石颗粒连续不断的进入系统。为维持系统床存量的稳定,需要连续的向系统外排物料。第五章 CFB锅炉主要性能参数及结构尺寸的计算及选择
116
因此,燃煤循环流化床对气体和固体均是个开口体系。如图
5-3所示,开口体系的平衡应当是对所有单独粒度的颗粒均
应达到平衡,即:
Gin(
i) = Gout(i)+ F(i) (5-3)
式中 Gin(
i)——燃煤成灰和石灰石给入带进系统的粒度为
di的物料流率;
F(i)——从分离器出口逃逸的粒度为di的物料流
率;
Gout(
i)——循环流化床排渣形成的粒度为di的物料
排渣流率;
X(i)——密相床内粒度为di的物料所占的比例;
E(i)——粒度为di的物料的夹带率。
而粒度为di的物料的夹带物料流应为
E(i)X(i),以夹带
物料流为基分离器效率为: s(
i) =1- F(i) /E(i)*X(i) (5-4)
则有:
F(i)=E(i)X(i) (1-i) (5-5)
同样以夹带物料流为基定义排渣效率为: o(i)= 1-
Gout(i) /E(i) X(i) (5-6)
系统对物料di的保存效率为:
m(i) = 1- [Gout(i)+F(i)] /[E(i)X(i)]= oi+i-1 (5-7)
再考虑物料平衡式有:
Gin(
i) = Gout(i)+E(i)*X(i)*(1-i) (5-8)
X(i)=1 (5-9)
上述方程组对于将颗粒分成任何数目的粒度档均可解。其中E(i)可以引用文献中的经验式
计算。总排渣率近似认为:
Gout=
Gout(i)/X(i) (5-10)
因此,无论进入循环流化床燃烧室中的物料粒度以及脱硫石灰石、外加床料的分布如何分
散,经过启动运行阶段,循环系统可对其进行“淘洗”,只有这种夹带率高,而分离效率亦很高
粒度的颗粒才可以在床内累计,使床料筛分形成一个很尖锐的峰。再看前文建议的系统对物料 Gin(
i)
Gout(
i)
F(i) X
(i) E(i) X(i)
5-3 第五章 CFB锅炉主要性能参数及结构尺寸的计算及选择
117
i
的保存效率m(i)为图5-4所示,系统保
存效率象一个山峰,左边细颗粒侧的形
状主要由分离器效率决定,右边粗颗粒
侧主要由排渣效率决定。床料分布的峰
顶恰恰对应系统保存效率的峰顶。
因此,循环流化床锅炉从启动到带负
荷的运行过程也是床物料累积和粒度逐
渐变细的过程。国外将床料平均粒度称
为“床质量”,并以此考察循环流化床物料
循环的好坏。循环流化床启动前填充的
冷床料粒度分布一般较宽较粗。刚刚运
行的循环流化床处于鼓泡床状态,密相
床表面有少量细颗粒扬析夹带。随着燃料煤的进入,生成灰份对床料进行补充,循环系统对物
料的淘洗,使得细物料所占比例逐渐增加,床料粒度下降,床质量提高。它反过来使颗粒夹带
逐渐增加。当夹带超过快床的最小夹带,即最小固体循环量,则循环流化床进入快床状态。若
循环量继续增加,则床层空隙率沿高度分布除逐渐增加外,床层下部还会出现细颗粒浓相区。
根据清华大学所作的研究,对于目前主流循环床技术,满负荷运行的循环流化床床存量中,可
夹带的细颗粒循环物料应当有500mm水柱既可以满足达到上部为具有颗粒团聚行为的快速床
状态。床存量多余部分是为了保证大颗粒有足够停留时间完成燃尽而设置的。
因此可以建立宽筛分给煤条件下循环流
化床锅炉的一维物料平衡模型,但是其基础是
必须考虑燃煤成灰特性,磨耗特性,否则其计
算结果必然因为对对象的过度简化而失真,法
国EDF公司在对Provence 250MWe 循环流化
床锅炉的计算曾经遇到这一问题。图5-5为
Provence 250MWe 循环流化床锅炉的模型预
测结果和现场测试结果的比较。若考虑物料磨
耗的因素,同时重点研究影响物料平衡的几大
因素,包括特定煤种的成灰特性和磨耗特性,
颗粒停留时间、颗粒分层、分离器效率等,可
以对循环流化床锅炉的主循环回路的物料进
行平衡计算。
工程上,要实现物料平衡,可以采用经验的方法,例如对一些主要参数,通过实践经验数
据的积累,确定下来。但是对于一些特定的燃料,如果没有实践经验,则应进行详细地分析计
0
20
40 60
80
100
0 500 1000 1500
颗粒粒径 m 效率
% 分离效率
排渣效率
系统保存效率
床料 床料
累计质量份额 % 0
20
40
60
80
100 5
-4
5-5 Provence 250MWe CFB
第五章 CFB锅炉主要性能参数及结构尺寸的计算及选择
118
算研究。
5.2 CFB锅炉性能参数和结构尺寸选择确定是保证锅炉达到设计出力和设计保证值的重要步
骤,关系到锅炉运行的安全性和经济性,直接影响锅炉厂的信誉和发展。
性能参数和结构尺寸与锅炉的容量、燃用的煤种和结构特性有关,随着锅炉容量的升级,
有些参数也要相应的发生变化。
以下针对100MWe到150MWe以下的CFB锅炉作分析讨论,所推荐的计算式及选择范围
供参考。
5.2.1
燃料破碎粒度是锅炉性能设计时首先要确定的性能参数。
对于CFB锅炉而言,“煤质”不仅指煤的成分,还包括入炉煤的破碎粒度,实践证明两
者都对锅炉本体及辅机的安全、可靠运行有影响,同时也对锅炉的性能参数有影响。
在尽量降低颗粒扬析的情况下,适当减少燃煤粒径,缩小筛分范围是提高燃烧效率和锅炉运
行安全性的有效措施。
锅炉设计时一般限定最大允许粒径(dmax)
、中径d50(定义为其上下各占50%重量的直径)和
小粒径的数量,表5-1示出了某公司推荐的入炉煤粒度要求。 5-1
煤种 褐煤 烟煤 贫煤 无烟煤
Vdaf
% 45~60 38 17 12 5
Aar
% <15 >15 <15 >15 - - <15 >15
最大粒径
dmax
mm 15 6 11 6 4 3 1.7 1.7
中位粒径
d50
mm 7 3 3 1.8 1.4 1 0.7 0.7
10%通过的孔径
d90
mm 1 0.5 0.5 0.42 0.2 0.2 0.2 0.2 表示煤的宽筛分破碎粒度用图示方法更简便。图5-6、5-7是某公司对几种煤的破碎粒度
建议。
从表5-1及图5-6、5-7中可见,随着煤的干燥无灰基挥发分减低,其破碎成灰能力变差,
燃尽度也降低,因此要求入炉煤粒度更细,只有这样,才能使床料(含煤粒)在炉内形成合理的
循环流率及灰浓度分布,满足燃烧、传热以及燃尽度的要求,并且为冷渣器提供适合其正常运
行的底渣粒度级配。另外,高灰分的燃料宜采用细一些的颗粒尺寸以便燃尽,改善在冷渣器中
的流化质量。但是由于我国的燃料供应问题,用户要求放宽粒度要求,因而远远超出理想的粒
度级配范围。 第五章 CFB锅炉主要性能参数及结构尺寸的计算及选择
119
5-6
Aar<15% 5-7 Aar>15%
第五章 CFB锅炉主要性能参数及结构尺寸的计算及选择
120
表
5-2列出了某厂贫煤135MWe锅炉入炉煤的粒度级配的设计要求及实测值。可见实际
入炉煤粒度偏离了设计要求(该要求已按用户意见放宽了),与规范相差更大,即细粒子份额多,
粗粒子份额也多,能形成有效循环的床料偏少。 5-2
135 MWe dmax,mm d50,mm d<0.2mm占的份额,%
技术规范
4 1.3 <10%
锅炉厂要求
7 0.6 <25%
实测值 d>7mm占3%
~0.25 44.6% CFB
锅炉的床料粒度级配受两个因素制约:除入炉煤的粒度之外,还有煤的成灰特性。
由于不同煤种的成灰特性差别较大(随挥发分、水分的增加,煤的热爆性增强,其次破碎程度
增加)。因此,要想在炉内形成合理的床料粒度级配,必须根据煤的成灰特性及燃尽特性来选
择入炉煤的破碎粒度。
石灰石既用于脱硫又起循环物料作用,要求石灰石粒径为0~1mm,切割粒径d50=~250
m;
在循环床燃烧温度区间内石灰石脱硫是
扩散反应,如石灰石粒径太大,比表面积
小,脱硫反应不充分,石灰石利用率低;
同时,颗粒扬折率也低,不能起到循环物
料作用。若颗粒太小,则在床内停留时间
太短,脱硫效果也差。石灰石宜用密闭系
统单独送入炉前石灰石仓中,然后送入燃
烧室。清华大学推荐石灰石粒度应满足图
5-7的要求。通常,国外公司要求石灰石
破碎粒度dmax<1mm
,d50<0.2mm,10%通
过的筛孔径<0.1mm。而国内则放宽了要
求,取dmax=1~1.5mm
,d50=0.2~0.45mm。
循环流化床的特点是对燃煤的粒度要求有个适应的范围,但是中国的国情是劣质煤、灰分
大的煤较多,而且由于资金问题,煤的制备又达不到要求,对流化床的燃烧和渣的冷却带来不
利的影响,为适应中国国情经专家讨论提出了对中国煤入炉煤粒度范围的建议,见本章最后表
5-14。用线图表示的入炉煤粒度见图5-30~图5-38。
5.2.2 Vy
烟气体积Vy是指每一公斤燃料完全燃烧,并考虑一定的过量空气量后产生的烟气体积,
m3(
标态)/kg。加石灰石后,理论空气量V0和烟气体积Vy均有所增加,但是其增加量不大。其
计算式如下: 0
25
50
75
100
02004006008001000
筛孔 m筛上余量
% 5
-7 第五章 CFB锅炉主要性能参数及结构尺寸的计算及选择
121
Vy=0
OH2V+0N2V+
VRO2+(1+0.0161)(α-1)V0,m3(标态)/kg (5-11)
干烟气体积Vgy:
00
N
RO
gy)
1(2
2V
VVV, m3(标态)/kg (5-12)
式中: 0
OH2V=0.111Har+0.0124(
Mar+B
BSh·Msh)+0.0161
V0,m3(标态)/kg; (5-13) 0
N2V=0.79
V0+0.8100
Nar,
m3(标态)/kg; (5-14)
VRO2=1.866100
)1(S375.0Cs
arar+(
CaCO3/100+
ηMgCO3/84.31)B
B
100
4.22Shm3(
标态)/kg (5-15)
V0=0.0889(Car+0.375Sar)+0.265Har-0.0333Oar+0.0167Sars m3(
标态)/kg (5-16)
式中 Car,
Har,Oar,Nar,Sar,Mar——每公斤燃料中碳,氢,氧,氮,硫及水分含量,%;
α——炉膛出口处过量空气系数,当求排烟处烟气体积时应取排烟处αpy;
Bsh——石灰石耗量,
kg/s;
Bsh=3.125
KSSarB3caco1,kg/s; (5-17)
Msh——石灰石中水份额,
%;
Ks——钙硫摩尔比;
CaCO3——CaCO3在石灰石质量中所占份额,%; MgCO3——MgCO3在石灰石质量中所占份额,%; s——脱硫率;
B——煤耗量,kg/s;
0.0167Sar×
ηs——炉内进行石灰石烟气脱硫时增加的理论空气量;
-1.866×100
375.0s
ars——脱硫减小的SO2烟气量。 注: ①计算中未考虑Sar的转化率K,若考虑的话,Sar应乘以转化率K(=0.9);
②计算中未考虑脱硫石灰石中碳酸钙分解率β,若考虑的话,应将Ks乘以
β(=0.95~1)。 5.2.3
炉膛空截面流动速度是指作为流化介质的空气或烟气流过炉内空截面(假想没有物料)时
的流化速度。 第五章 CFB锅炉主要性能参数及结构尺寸的计算及选择
122
空截面流化速度影响炉膛内温度分布、物料的循环流率及烟气在炉内的停留时间,从而影
响炉内的传热率、锅炉设计尺寸和运行性能。
(1) 密相区空截面风速Wm
CFB锅炉炉膛下部固体颗粒较粗且浓度较高的区域称为密相区。
密相区的具体尺寸各家说法不一,为了计算方便,建议统一按下述定义考虑:从布风板到
下数第一层二次风中心截面为密相区;从第一层到最后一层二次风中心截面为过渡区,上二次
风以上到炉膛出口为稀相区。
密相区空截面风速Wm是指流过密相区布风板上空截面
(假想无物料)时的气流速度。
对于一定的煤种及颗粒度,Wm由下式计算:
Wm=273
2731
1
0
j1pjmb
a
VBr
p
325.101
m/s (5-18)
式中:r1——
一次风率;
P——计算区的平均床层压力,kPa;
P=101.325 + P,表压 kPa (5-19)
当需要进行海拔高度(H,m)修正时,修正后的床层压力P′按下式计算:
P′=101.325(1-0.02257 H /1000)5.256+
P表压,kPa (5-20)
Bj——
计算煤耗量,kg/s;
V0——
理论空气量,m3(标态)/kg;
θpjm—
密相区烟气平均温度,℃
α——炉膛出口过量空气系数;
a1b1——
布风板截面尺寸,m2。
按理说,密相区流化速度应按烟气速度计算,但是计算烟气速度需要知道密相区释热份额
δ,此性能参数δ较难于准确确定,故采用密相区风速来代替,而其温度按烟气平均温度计算。
一般Wm取等于
4.2~5.2m/s范围。
(2) 稀相区空截面烟气速度Wx CFB锅炉炉膛上二次风中心以上颗粒较细且浓度相对较低的气固两相流区域称为稀相区。
稀相区空截面烟气速度Wx是指流过稀相区空截面
(假想无物料)时的平均气流速度。
Wx=炉膛截面积
全部烟气体积=p
ab
VB
325.101
273
273pj
yj
,
m/s (5-21)
式中 Vy——烟气体积,
m3(标态)/kg; 第五章 CFB锅炉主要性能参数及结构尺寸的计算及选择
123
Bj——计算煤耗量,
kg/s;
θpj——
炉膛内烟气平均温度,℃;
ab——炉膛截面尺寸,m2;
P——计算区的平均床层压力,P=101.325+P表压,
kPa,当需要进行海拔高度修正时,参
考式(5-20)。
稀相区烟气速度Wx一般取
4.6~5.5 m/s范围,稍高于密相区流化风速Wm。通常,密相区
空截面风速Wm与稀相区空截面烟速
Wx基本相同,称为等流速变截面设计,则炉膛内的烟气
流速可以用稀相区烟速代表。
5.2.4 τ
对于循环床来说,中等颗粒物料在炉内多次循环,故停留时间较长,而一些小颗粒则随着
烟气只经过炉膛一次就由分离器排到尾部受热面去,造成飞灰可燃物损失。
(1) 烟气(包括细小颗粒)在炉内的名义停留时间
定义为在一定的温度和压力下烟气均匀地充满和流过整个炉膛所需的时间。烟气(不考虑
滑移速度时炉内细小颗粒的上升速度与烟气速度相同)在炉内的停留时间长短将一定程度影响
q4值及锅炉效率
η。
烟气(细小颗粒)名义停留时间:
x
2*
W
h口的高度从布风板表面到炉膛出
(5-22)
式中 h2*
——柱体的高度h2Z+锥体的高度h2x。锥体的高度应折算为柱体体积时的高度,但是
在锥体阶段热释份额低,故烟气量也低,所以烟速维持基本不变,故不需折算。
Wx——稀相区烟气速度,
m/s。一般τ取为5~7秒。
如果考虑颗粒与烟气的滑移速度,则式(5-22)中的分母Wx应减去滑移速度
Wslip(取等于颗
粒终端沉降速度ut)
,则其停留时间增长。
假定平均颗粒直径为90m,则沉降速度Wslip≈
0.2 m/s,这时的烟气(包括细小颗粒)的名
义停留时间将增长0.2~0.3秒。
当采用高温分离器时,在分离器大部分容积内的停留时间也应算是燃料在炉内的停留时
间,特别是对于低Vdaf燃料,在一定条件下分离器出口温度高于入口温度,说明在其中还有燃
烧过程。如果考虑这部分时间,则式(5-22)所得的时间应有所增多,可由下式表达: 2
xsliph*
WW
从布风板表面到炉膛出口的高度 (5-23) 式中
δ——大于1的修正系数,对于典型的CFB锅炉,δ=1.23~1.44。 第五章 CFB锅炉主要性能参数及结构尺寸的计算及选择
124
(2)
外循环物料在炉内的平均停留时间τwl
外循环物料中粒径小于分离器临界粒径的物料经过一次循环即被排放到尾部烟道去,如前
节所述。而大于临界粒径的物料则返回到炉内进行再循环,其循环次数n决定于分离器效率ε,
即
100
100
n (5-24)
如分离器效率ε为
99.5%,则n=200次,则总共的
停留时间τwl为nτ
秒。即如果一次的停留时间是6 s,则
总共τwl=6
×200=1200 s。
(3) 物料在炉内的平均停留时间τxh
将炉膛分为图5-8所示的假想分界线上下两部分,上
部分为细颗粒的物料循环,下部分为大颗粒的流化,并假
定上部分(包括分离器内)的物料存量为InV1 kg,
下部分的物
料存量为InV2 kg
,排渣量为BLZ kg/s。飞灰量为Bth kg/s,
则细颗粒在炉内上部的停留时间为: 1
xh1
thINV
B (5-25)
粗颗粒在炉内下部的停留时间为: 2
xh2
lzINV
B
(5-26)
τxh1决定了飞灰可燃物含量,而
τxh2决定了底渣的可燃物含量,减少飞灰量可以提高细
颗粒的停留时间,减少底渣量可以提高粗颗粒的停留时间,若Go
lc代表外循环流量,分离器的
效率为εfL,则
2
oo
LCCfLCfLLCπ
4
d
GGGabGN (5-27) thsfL1
BGab (5-28)
式中 GC——基于床截面积的炉膛出口物料流率,
kg/m2;
GLC——基于料腿截面积的物料流率,
kg/m2s;
N——料腿数量,个;kg/s;
d——料腿直径,m。
(4) 煤粒在炉内燃尽需要的停留时间τx理论计算
5-8
第五章 CFB锅炉主要性能参数及结构尺寸的计算及选择
125
对于褐煤及高挥发分烟煤一般在炉内的停留时间足以达到所需要的燃尽度,而对于低挥发
分的贫煤、无烟煤则燃尽时间总显得不足。故下面针对低挥发分煤进行分析。
考虑低挥发分煤焦碳颗粒燃烧时不膨胀,可按等径缩核机理处理。对于细小煤焦碳粒子(dp≤
200m),认为周围氧气浓度对其燃烧速率影响不大,扩散对粒子的总体燃烧速度影响很小,
燃烧过程由表面反应速度控制,燃烧速率为化学反应速度。若忽略焦碳的磨耗,由质量平衡: 2
O,2)
/exp(
d
d1
dCRTEA
Mc
Mcp
(5-29)
取碳颗粒温度等于燃烧室温度(Tp≈
Tg),并假定A=k0 Tp,CO与CO2生成比例为1:1(Ψ=4/3),
氧气浓度按炉膛内平均值计算;则积分上式可得细颗粒的燃尽时间为: 2O
,0)/exp(2
CRTETMck
dg
g
ps
x
(5-30)
式中,Ψ=4/3;R=8.314 J/mol·K
;Mc=12 g/mol;C∞,O2=6.25 mol/m3,则式(5-30)可简化为 )]314.8/(exp[
50
gg
ps
xT
EkT
d
(5-31)
取煤的活化能与挥发分Vdaf的关系式为
E=313734-60799.ln Vdaf J/mol (5-32)
计算结果见表5-3。由表5-3看出,对于低挥发分煤,挥发分对燃尽的影响非常敏感。当
Vdaf为
15%、烟温取900℃时需要6.28 s;而当Vdaf为11%、烟温取900℃时就需要29.0 s。如
果将烟温提高到950℃时则停留时间可减少到13.8 s。可见对于低Vdaf煤种应取高的烟气温度
和高的炉膛实际停留时间才会有利于燃尽。 5-3
Vdafτx
序号 名称 符号 单位 A电厂 B电厂 C电厂 D电厂
1
颗粒密度 ρs
kg/m3
2000 2000 2000 2000
2
颗粒直径
dp
m 0.0001 0.0001 0.0001 0.0001
3
烟气温度
Tg
K 1173 1173 1173 1223
4
频率因子
k0
m/s 595 400 890 890
5
挥发分
Vdaf
% 15 17.12 11 11
6
活化能
E J/mol 149087.1 141049.6 167944.3 167944.3
7
燃尽需要时间 τx
s 6.28 4.1 29 13.78 实际应用时煤的活化能不易得到,下面给出一个简易经验公式(见式
5-30a)
τ=6.067×108×
EXP(-0.01276Tp) ×dp1.16 (5-30a)
dt--煤粒的初始粒径 mm; 第五章 CFB锅炉主要性能参数及结构尺寸的计算及选择
126
T--
炉内平均温度 k。
根据上面公式(5-30 a)作出下表(5-3 a ) a ℃
μm 25 50 75 100 150 200
800 9.52 21.27 34.04 47.52 76.06 106.2
850 5.03 11.24 17.98 25.11 40.18 56.1
900 2.66 5.94 9.50 13.26 21.23 29.64
950 1.4 3.14 5.02 7.01 11.22 15.66
970 1.09 2.43 3.89 5.43 8.69 12.13
1000 0.74 1.66 2.65 3.7 5.93 8.27
由表可见,随着炉膛温度水平的提高以及粒子直径的减小,粒子的燃尽时间减小。 当然,燃烧进程还与颗粒的氧气供给密切相关,上述计算中忽略了炉膛中的混合问题。事
实上CFB炉膛中的混合问题很重要。若混合效果不佳,燃尽时间将有很大的增加。由上表可
见,细粒子在炉膛内的停留时间一般应大于6秒。 5.2.5 r1 一次风率指从布风板底下加入的风量占供给锅炉炉膛燃料燃烧所需总风量的比例。为增加
穿透能力(一次风压头高于二次风压头)个别CFB锅炉设计也有将部分一次风从布风板上部送
入,作为最下层二次风。
一次风率对密相区的热量释放份额(燃烧份额)起着决定性作用,在同样的燃料特性和流化
速度条件下,一次风率越大,燃料在密相区的热量释放份额也就越大。在密相区由于一次风量
仅是燃烧所需风量的一部分,故形成还原气氛,这有利于降低NOx的排放量。
不同型式的锅炉,其设计工况不同,故一次风率也不同。一般为45%~55%。此外,一次
风率的选取也要考虑燃料粒度和性质因素,对于难燃燃料一次风率应选高值,一次风率过小会
增加不完全燃烧热损失,对于高挥发份燃料一次风率可选低值。清华大学认为一次风率r1选
取应根据燃料燃烧单位烟气量释放的热值,并根据燃料中挥发分含量确定,对于煤,建议一次
风率r1等于daf66
3
V
,%。表5-4给出几家锅炉公司采用的一次风率。 5-4
Ahlstrom Lurqi Battelle Circofluid Studsvik
~50% 40%~50% 40% 60% ~45% 普华专家研讨会建议的一次风率见表
5-14。
5.2.6 r2W2 采用一、二次风分段送入有利于降低
NOx的生成,特别是对于高挥发份煤种。二次风可
分成2~3层从布风板以上1~5 m处送入。要选择合适的二次风速w2及二次风出口动量
mw2,
以达到足够的穿透深度,一般二次风速取60~100m/s。需注意,给煤系统、冷渣器、回料器、第五章 CFB锅炉主要性能参数及结构尺寸的计算及选择
127
换热床及输送石灰石都需要用风,故确切来说
r2≠100 -r1,一般一、二次风总和为总风量的≈
94%。
5.2.7 θ1θ2 由于循环床锅炉床层的大量蓄热,对煤的着火不成问题,故一、二次风温的选取主要考虑
给水温度以及排烟温度的经济性,兼顾燃烧室中的热平衡,一般取150~250℃。对低挥发份或
高水分燃料可取稍高的温度。
5.2.8 δ
密相区的定义为从布风板到最下层二次风中心截面以下区域。
密相区热量释放份额δ定义为燃料在密相区燃烧释放出的热量占全部燃料输入热量的比
例。由于密相区燃烧产物中有大量的CO、CH等物质,并未完全燃烧,因此采用“热量释放
份额”较之“燃烧份额”更为合理。为便于理解,本书不区分燃烧份额和释热份额。
密相区内的热量释放份额与燃料特性、床料粒径、流化风速、一二次风率、床层温度、煤
中挥发分含量等有关。
图5-9给出了流化风速与密相区燃烧
份额的关系。从图中可以看出,当粒径一
定时,风速增加,密相区的燃烧份额下降。
这是很明显的,由于风速增加,颗粒被吹
起进入稀相区的份额增加,所以密相区的
燃烧份额下降。
图5-10给出了密相区燃烧份额与稀
相区平均温度的关系。从图中可以看出,
当颗粒尺寸较小时,稀相区平均温度增
加,稀相区燃烧反应速度加快,从而使稀
相区燃烧份额增大,密相区燃烧份额下
降。图5-9和图5-10同时还给出了密相区
燃烧份额与燃料粒径的关系。
从图中可以看出,当粒径增大时,密
相区的燃烧份额增大,因为粒径增大,停
留在密相区的颗粒量会增大,从而使密相
区内的燃烧释热份额增大。
当锅炉负荷增加时,密相区的释热份
额下降,这是由于为了维持密相区的床层温度,在低负荷时必须增加密相区的释热份额,而在
5
-9 5-10 第五章 CFB锅炉主要性能参数及结构尺寸的计算及选择
128
高负荷时为了防止床层超温,必须降低密相区的释热份额,为此一般通过调节一二次风配比来
实现。
在循环流化床锅炉的设计中,常常用到调节一二次风配比来调节密相区的释热份额。增加
一次风比例,密相区的释热份额会有所上升,但增加的份额远低于一次风 增加的比例。在循
环流化床锅炉中,二次风一般在稀相区给入,所以二次风不可能参与密相区的燃烧,此时一次
风的比例一般就是密相区释热份额的最大值(当然此时的过量空气系数不应过大)。有时为了控
制密相区的释热份额,就采用降低一次风率
的办法来达到。
煤中挥发分对释热份额的影响最为明
显。图5-11是燃用焦碳和烟煤两种情况下燃
烧室内释热份额沿床高的分布曲线。由图可
见,焦碳在密相区中的释热份额明显高于相
近实验条件下烟煤在密相区的释热份额,表
明烟煤中的挥发分很大一部分被带到了稀相
区进行燃烧。
5.2.9 θcc
床层温度θcc是指密相区流动介质的平均温度。
床层温度θcc是
CFB锅炉运行主要控制参数之一。床温高有利于强化燃烧和传热,有利于
提高燃烧效率,特别是对于难燃煤种,如无烟煤更是如此。但床温上限受到灰的变形温度的限
制,同时较高的床温将导至NOx排放量增加。另外,要考虑脱硫加石灰石所需的最佳温度为
850~870℃,与煤种有关。故当燃用硫分较高煤种时,考虑脱硫效果兼顾高效燃烧,床温可取
850~900℃。如果燃用的燃料硫分较低,特别是低挥发分煤种,则床温可适当提高,一般可取
900~920℃。
锅炉设计时具体的床层温度应该通过炉膛分段传热计算求得,但分段计算时如释热份额等
影响因素较难确定,故有的公司则根据运行经验确定:取满负荷时与炉膛出口温度相等,低负
荷时床温要比炉出口温度降低的少;有的公司在满负荷时床温就比炉膛出口温度高出十几度。
根据我国的运行数据看,取床温与炉出口温度相同是理想的状态,而一般总是床温要高于炉出
口温度。
床层温度一般由炉膛前墙及侧墙分几层伸进几个热电偶测出。为保证测量的精度CFB炉
膛中热电偶伸出长度不应小于100mm。由于此处水冷壁均有耐火耐磨涂料,故较少影响测量
值,但是磨损较为严重。另外也有从布风板底部的风室分几处伸进到床层中来测量床温,这样
可以测到床层中心处温度,不过热电偶的维护不如前者方便。 5
-11 第五章 CFB锅炉主要性能参数及结构尺寸的计算及选择
129
5.2.10
θL
″θfl″
(1) 炉膛出口温度θL
″
炉膛出口温度θL
″指炉膛出口处的介质平均温度。
炉膛出口温度的选取原则与影响因素基本与床温相同,一般设计其数值可与床温相当,或
者稍低于床层温度。出口温度低则炉膛高度增加,金属耗量增加,但烟气停留时间增加,燃烧
效率提高。出口温度应是合理的设计值,运行中需要由主循环物料的性能,燃料粒度等来实现。
CFB锅炉的特点是有大量的物料在炉内炉外进行循环,特别是内循环,结果导致炉膛内
各点的烟温趋于一致。不存在煤粉炉那样有一个温度较高的燃烧中心。
(2) 分离器出口烟气温度θfl
″
CFB锅炉炉膛出口烟温不等于尾部烟道入口烟温,即使是绝热型旋风分离器。因为炉膛
出口处的物料中含有未燃碳,在分离器中有可能继续燃烧,从而使烟温高于炉膛出口烟温。
如第三章所述,细碳粒子在分离器继续燃烧的现象称为“后燃”。后燃如果不造成结渣及
分离器内耐火层脱落等问题,则可认为是正常现象,若把分离器当成炉膛燃烧的空间,则后燃
可看成是一件好事。但是对于低挥发分煤种,经常出现的“后燃”现象,使绝热分离器出口的
烟气和回料温度高于入口温度,国内已投运的135MWe级贫煤CFB锅炉其温差△t可达
30~70℃,负荷越高,越接近上限,而燃用褐煤的电厂其温差为0甚至为负值。如果锅炉设计
时未考虑“后燃”现象,则“后燃”会使尾部烟道入口烟温升高,增大尾部过热器的吸热量,
使之超温和喷水量过大,同时也提高了排烟温度。
当采用汽冷式、水冷式旋风分离器时后燃现象可能减少,同时有利于防止易结渣煤种在分
离器内结渣。对于低Vdaf的煤种,如果事先考虑到后燃现象,可采取防结渣措施。
5.2.11 PCCPFS
床层压力PCC是指在布风板出口处测出的静压
(表压)平均值,风室风压PFS指在风室内测出
的静压(表压)平均值。
床层压力PCC是
CFB锅炉运行控制的主要参数之一,它与许多因素有关,如颗粒粒度、床
层高度、密相区流化风速及床温等。
床压测点沿炉膛高度可布置三层,最低一层床压测点一般布置在布风板以上200~225 mm
处,再低受风帽的影响不易测准,最高点约为布风板以上5000 mm处,运行时床压一般指最
低一层测出的静压。
布风板的阻力一般应为风室风压与炉膛出口压力差的1/3到1/2左右,以防漏渣。通常风
室风压与炉膛出口压差为12000~15000 Pa,故若布风板阻力为~6000 Pa左右,从布风板到床
层压力测点处还有200 mm多的阻力损失(大约为2500 Pa左右),所以风室风压约等于床压和
二段阻力之和,即测出的床压(~6000 Pa),200 mm的阻力损失(~2500Pa)和布风板阻力(~6000 Pa)第五章 CFB锅炉主要性能参数及结构尺寸的计算及选择
130
总计大约为
15000 Pa左右。
5.2.12 h1 运行状态下的流化床床层高度很难确定,没有明显的分界线,故一般床层高度指布风板以
上颗粒较粗、密度较大的颗粒物料层。
静止状态下一般取0.5~0.8 m, 对于300MWe CFB锅炉可取1.0m,床层太厚则床压增高;
床层太薄,燃烧不稳定。对于低挥发分或低热值燃料应取高值,以提高燃料着火稳定性及维持
高床层温度,有利于燃烧和燃尽。
膨胀状态下的床高是静止状态下的2~2.5倍。
5.2.13 Wfl′
如果已知炉膛稀相区空截面烟气速度Wx,则旋风分离器入口烟速
Wfl'=
WxNba
ab2
2,m/s (5-33)
式中 ab——炉膛截面尺寸,m2;
a2b2——
分离器入口截面尺寸,m2;
N——分离器个数,个。
需注意,有的分离器入口后有一个加速段(收缩段)。因此,其入口速度应等于收缩后截面
积按上述式(5-23)计算出的数值。目前分离器入口速度一般取20~25 m/s。
5.2.14 ηfl
旋风分离器分离下来的物料量与进口物料量之比称为分离器效率。分离效率通常又分为总
分离效率ηfl与分级分离效率
ηi。两者的关系是:
ηfl=
∑ηixi (5-34)
式中 xi——入口颗粒筛分特性,即某一种颗粒量占总量的份额。
旋风分离器是CFB锅炉中的重要部件,是影响主循环回路工作性能的关键之一,它的分
离效率高低将直接影响传热效果和运行成本。影响分离器效率的因素有分离器本身结构尺寸
(包括中心管长度和直径、分离器直径等)、入口物料速度、物料颗粒粒径及颗粒浓度等。
ηfl高低直接影响物料的循环流率
Gs,继而影响炉膛出口烟气对固体物料的携带率Mfl及物
料浓度CP,从而影响炉内的传热,另外
ηfl高低还影响飞灰可燃物的高低,影响飞灰底渣比,
影响锅炉效率。
有关分离器的设计和效率计算见旋风分离器一章。
国外设计ηfl通常取用
>99%~99.5%,这对于稳态运行过程,由于物料循环系统颗粒已经经第五章 CFB锅炉主要性能参数及结构尺寸的计算及选择
131
过积累,是可能达到的,但实际运行结果有待进一步验证。
5.2.15 afh 飞灰份额
afh指从锅炉尾部飞出的灰分占锅炉排出总灰分(包括石灰石添加剂形成的灰分)
的比例。一般锅炉排灰分两部分,一部分为飞灰份额afh,另一部分称底渣份额
adz,%,两者
相加afh+
adz=100%。
afh与煤的灰分及其性质、颗粒粒径、密度、流化风速、分离器效率、炉型及运行方式有
关。某引进技术公司规定,在干燥基灰分<20%时取煤灰的afh为
60%;当干燥基灰分>20%时
取afh为
45%;加石灰石脱硫产生的afh为65%,两者应加权平均。
以440 t/h锅炉为例进行计算:
燃用燃料Aar=18.64%
;Mar=7.35%;B=14.63kg/s;Bsh=0.65kg/s;
燃料干燥基灰分Ad=
Aarar100
100
M=19.92%
440 t/h锅炉的灰量BA
ar=14.63×0.1846=2.7 kg/s
以BA
ar和Bsh来加权则
afh=%
6161.0
65.07.2
65.065.07.26.065.06.0sh
ar
shar
BB
BBA
A
按此法计算某465 t/h锅炉afh=62%
;某450 t/h锅炉afh=50%。
另外,飞灰与底渣量比还与煤种有关。褐煤灰的比重轻,故其飞灰量大于贫煤,表5-5给
出一个经验值(未考虑石灰石)。 5-5
()
煤 质 褐煤 烟煤 贫煤
灰分Aar/%
<20 >20 <20 >20 <20 >20
飞灰/底渣
70/30 60/40 60/40 50/50 55/45 40/60 5.2.16
Gs
物料循环流率Gs定义为颗粒循环流量与炉膛截面积之比,这是
CFB锅炉的特征参数之一。
对于一台设计好的锅炉在其它参数不变的条件下改变燃用煤种时,必须保持循环流率Gs不变,
才能维持原有的锅炉负荷。
在CFB锅炉中的物料循环又分为内循环与外循环。
通过分离器分离下来的循环流量0
LCG与炉膛截面积
F之比称为外循环流率。在不特殊说
明的情况下物料循环流率就是指外循环流率GS
第五章 CFB锅炉主要性能参数及结构尺寸的计算及选择
132
0
LC
sG
G
F
kg/m2·s (5-35)
式中 0
LCG——颗粒外循环流量,
kg/s;
F——炉膛截面积,m2。
在已有的国内CFB锅炉书籍和文章中常用到循环倍率R的概念。循环倍率是在解决鼓泡
床燃烧效率采用飞灰(从除尘器下获得的低温飞灰)再循环时描述回送飞灰量的概念,在此情况
下飞灰回送回炉膛是作为燃料用的,因此与燃料之比定义为循环倍率。而在循环流化床中不同,
循环流化床自身的定义为循环流化,而非循环燃烧,故这里不提倡循环倍率概念,而在描述飞
灰再循环时在循环流化床锅炉中仍然使用循环倍率概念。
考虑到已有文献中或人们的头脑中仍有循环倍率R的概念,故这里给出外循环流量0
LCG与
循环倍率R的关系式: 0
LCG°=
R (B+Bsh) (5-36)
式中 B——煤耗量,kg/s;
Bsh——石灰石耗量,
kg/s。
同时也把循环倍率的推导过程附注于后面。
附注:关于物料循环倍率R的讨论 文献上对循环倍率
R有许多不同的定义。这里取用R为循环物料量与(煤耗量+石灰石耗量)之比:
R=
shfhfl
sharfhfl100
100
100
BBC
BAAa
(5-37)
式中 αfh——飞灰份额;
fl——分离器效率,%;
Aar——燃料灰份,
%;
Cfh——飞灰可燃物含量,
%;
Ash——加入石灰石后增加的灰量,
kg/kg(煤);
B——实际煤耗量,kg/s;
Bsh—
石灰石耗量,kg/s。
影响循环倍率的主要因素有:燃煤的灰分、石灰石耗量、燃煤和石灰石尺寸及其粒度分布、流化速度和
分离器的效率等。分离器效率ηfl对
R的影响极为敏感。
循环倍率的选取是循环量选取结果的一种表述,要考虑燃烧效率及脱硫效率;还要考虑分离器磨损及引
风机的能耗,根据燃料热值的不同,循环倍率一般为20~40。
第五章 CFB锅炉主要性能参数及结构尺寸的计算及选择
133
循环倍率R的推导:
设分离器效率为ηfl,
ηfl是由分离器回来的物料量0
LCG与进入分离器的物料量0
CG之比,即
ηfl=1000
C
0
LCG
G,
% (5-38) 0
CG=
αfh(Aar+100Ash)Bfh100
1
C+ 0
LCG (5-39) 0
CG根据循环倍率的定义:
0
CG=(
B+Bsh)·R (5-40)
将式(5-39)、(5-40)代入式(5-38)式得
η=
R
BB
C
BAAa
RBB
sh
fh
sharfh
sh100
1
100
100 (5-41)
由式(5-41)式可求得
R
sh
fh
sharfh100
100
100
BBC
BAAa
(5-42)
说明:式中分子Ash前边乘
100,是因为原单位是kg/kg,是小数,而Aar是百分数。
将式(5-42)代入式(5-36)和式(5-37),可得外循环流率G°s
的表达式: FC
BAA
G
)100)(100(
)100(fh
sharfh
s
(5-43)
100~150MWe级CFB锅炉Gs在
4~9 kg/m2s范围内。
外循环流率还可用炉膛出口物料浓度Cp和炉膛出口物料流量
Gc来表达。 pp1C kg/m3 (5-44) Fu
u
Gt
x
pC
)
1(,kg/s (5-45)
t
x
p
flC
su
u
F
G
G
)
1(fL,kg/m2·s (5-46)
式中 ρp——物料的真密度,
kg/m3;
ε——炉膛出口处的空隙率;
ux——炉膛出口烟气速度,
m/s;
F——炉膛出口处床截面积,m2;
ut——炉膛出口处物料沉降速度,
m/s;
第五章 CFB锅炉主要性能参数及结构尺寸的计算及选择
134
fL——分离器分离效率。
假定:ρp=2200 kg/m3;
ε=0.999;ux=5 m/s;ut=1.1 m/s(取出口物料平均粒度=150m), εfL=0.99,则 5.899.01.1
999.0
5
)999.01(2200
sG kg/m2·s。 5.2.17 Mwl 炉膛出口处每千克烟气携带的物料千克质量称为物料携带率Mwl。100MWe~150MWe级
CFB锅炉的Mwl一般在
3~6 kg/kg范围内。
Mw1=4
fhy
fh
shar
0
lc100
100
100
100
100
100
qCG
a
AA
B
G
kg(
固体)/kg(烟气) (5-47)
式中 G0
LC——
物料外循环流量,G0
LC=
R(B+Bsh),kg/s;
Aar——
煤中灰分,%;
αfh——
飞灰份额,当加入石灰石脱硫时αfh增大;
Ash——
加入石灰石后增加的灰量,kg/kg(煤);
Ash=
MCaSO
4+McaO+
MMgO+M杂质 =33
3sararss
sar
CaCOMgCOsh00425001749
003125
4401
100
8431CaCO.S.SK
.KS
.
M
.
kg/kg(煤)
(5-48)
式中 MCaSO
4——
1kg实际燃料燃烧脱硫后产生的CaSO4量,kg/kg(煤);
McaO,
MMgO,M杂质——1kg实际燃料燃烧脱硫时未反应的CaO,MgO和石灰石的杂质
量,kg/kg(煤);
Ks——
钙硫比;
ηCaCO
3——
CaCO3在石灰石中所占份额,%;
ηMgCO
3——
MgCO3在石灰石中所占份额,%;
Msh——
石灰石中水份含量,%;
ηS——
脱硫率,取0.75~0.9;
Gy——
每公斤燃料的烟气质量,kg/kg;
Cfh——
飞灰可燃物,%;
q4——
固体未完全燃烧热损失,% 。 第五章 CFB锅炉主要性能参数及结构尺寸的计算及选择
135
fhC
100
100
——为考虑飞灰含碳量修正; 4100
100
q——为考虑计算煤耗量产生的烟气体积的修正。
物料携带率有时又称为固气比M 。其定义为任一截面处物料质量流率Gsolid与气体质量流
率之比,即 solidgG
M
u
(5-49)
式中 Gsolid——物料质量流率,
kg/m2·s;
ρg——气体密度
, kg/m3;
u——气体速度,m/s。
对于炉膛出口处 C
gG
M
u
(5-50)
M又可变换为 oo
CCC
gggGGG
M
uFuG
(5-51)
式中 o
CG——炉膛出口固体颗粒质量流量,
kg/s;
Gg——气体质量流量,
kg/s。
5.2.18 ()Cp 知道炉膛出口处的物料携带率
Mwl后即可求出炉膛出口物料浓度Cp。
Cp=
Mwlρpj
y273
273
kg/m3 (5-52)
式中 ρy——烟气密度,
kg/m3(标态);
θpj——烟气平均温度,℃;
以100MWe级CFB锅炉为例,假定Mwl=4 kg/kg
,θPj=883℃, ρy=)(kg/m34.1
21.8
5.62.1306.146.1801.01
y
306.101.013
ar标
V
VAO
则Cp=4×1.34×883273
273
=1.27kg/m3。
一般出口物料浓度为Cp=1~2 kg/m3范围或
Cp=2~5 kg/m3(标态)范围内。 第五章 CFB锅炉主要性能参数及结构尺寸的计算及选择
136
物料浓度
Cp还可用床层压差△P与高度差△H来求出: pp1
g
P
C
H
(5-53)
式中 ρp——物料密度,
kg/m3;
ε——空隙率;
△P——床压差,Pa;
△H——高度差,m;
g——重力加速度,m/s2。
5.2.19 q f
炉膛截面尺寸由所选取的流化速度决定,具体尺寸的选取应考虑受热面及分离器的布置,
考虑二次风的穿透能力,考虑燃料、石灰石及回灰的供给与扩散。炉膛深度一般最大不超过8 m,
必要时采取裤衩式结构,以确保二次风穿透深度。
截面热负荷与流化速度两者是相关的,因此流化速度确定后截面热负荷也就qf确定了。
qf=ab
QB
1000net,arjMW/m2 (5-54)
式中 Bj——计算煤耗量,
kg/s;
Qnet,ar——发热量,
kJ/kg;
ab——炉膛截面尺寸,m。
5.2.20 SO2
CFB锅炉炉温应保持在850~900℃温度范围,其显著优点之一是可实现高效廉价脱硫,一
般脱硫率在90%以上。SO2的排放浓度可通过给定脱硫率计算,过程如下:
① 1kg煤在炉内燃烧生成的二氧化硫质量(SO2)m:
kg/kg,0.018S0.9S0.02
100
0.9S
32
64
100
0.9S
)SO(arar
arar
s
so
m22
n
n (5-55)
式中 Sar——燃料含硫量,
%;由于一部分硫含在硫酸盐中,不参加反应,故将Sar乘以0.9。 2SOn——SO2的摩尔质量,kg/mol; Sn——S的摩尔质量,kg/mol。
② 不脱硫时SO2的排放浓度
CSO2′ gy
6
m2
SO10
)SO(
C2V
,
mg/m3(标态) (5-56) 第五章 CFB锅炉主要性能参数及结构尺寸的计算及选择
137
式中
Vgy——尾部排烟处(=1.4)的干烟气体积,m3/ kg(标态)。
③ 脱硫后SO2的排放浓度
C SO2 22SO
s
soC
100
-100
C
gy
6
ars10
S018.0
100
)-100(
V
mg/m3(
标态) (5-57)
式中 εs——脱硫率,
%。
式(5-57)是通过计算得出的CSO2浓度。在试验时实测的
CSO2浓度按下式计算: 22SO
2
soC2.86
O21
6-21
C
,mg/m3(标态) (5-58)
式中 CSO2″——实测干烟气中的
SO2体积浓度,L/L;
O2——实测干烟气中的含氧量,
%。
按2003年12月发布的火电厂大气污染排放标准要求,自2004年1月1日起新建、扩建、
改建的火电厂项目(包括燃煤及燃油炉)SO2的排放不得高于
400 mg/m3(标态)。为满足标准要求
应在燃烧中加石灰石脱硫,对于含硫量高的煤要求高的脱硫效率,Ca/S比也相对要高。
5.2.21 ηs
定义为不加脱硫剂时的SO2排放浓度
C′SO2减去加脱硫剂后的SO2排放浓度CSO2之差与不
加脱硫剂的SO2排放浓度
C′SO2之比,即 2
22SOsoSO
sC
CC
(5-59)
由式(5-57)可得出给定排放浓度CSO2后,需要的脱硫效率
εs ar
gysogySVCV
2
20055.0
100
10S0.018
100C
1006
ar
SO
s (5-60)
根据式(5-60)对几台100~ 135MWe级锅炉需要的脱硫效率计算结果见表5-6。 5-6
举例
锅炉出力
煤种
燃料中硫含量
Sar %
干烟气体积
Vgy Nm3/kg
给定的SO2排放浓
度
CSO2
mg/Nm3
需要的脱硫效率
εs
%
1
465t/h,烟煤
1.93 9.04 400 90.63
2
440t/h,贫煤
0.5 8.99 400 64
3
450t/h,贫煤
1.46 7.36 400 89.9
4
220t/h,贫煤
3.12 8.39 400 94.5
5
440t/h,褐煤
1.66 4.7 400 94.3 注:
Vgy按未加石灰石计算的,当加石灰石时会略有增加,因而脱硫效率会略有降低。 第五章 CFB锅炉主要性能参数及结构尺寸的计算及选择
138
5.2.22
Ca/S
为达到要求的脱硫率应在炉内掺烧石灰石。钙硫比Ca/S定义为钙的摩尔质量与硫的摩尔
质量之比。对于不同的燃料含硫量Sar和给定的脱硫率
εs,所需的Ca/S应根据经验确定,当
没有使用经验时可参考图5-12~5-15和后面的式式(5-61)计算。 石灰石流量
0
5
10
15
20
25
02004006008001000
SO2排放
/mg.Nm3石灰石流量
/t.h-10
5
10
15
20
25
灰渣中平均CaO含量灰中
CaO
含量
/% 脱硫效率
80
85
90
95
100
02004006008001000
SO2排放
/mg.Nm3脱硫效率
/%0
1
2
3
4
5
钙硫摩尔比钙硫摩尔比
5-12 SO2CaO
(Sar=2%, Aar=25%, Qar,net=22MJ/kg) 石灰石流量
0
5
10
15
20
25
02004006008001000
SO2排放
/mg.Nm3石灰石流量
/t.h-10
10
20
30
40
50
60
灰渣中平均CaO含量灰渣
CaO
含量
/%脱硫效率
90
92
94
96
98
100
02004006008001000
SO2排放
/mg.Nm3脱硫效率
/%0
1
2
3
4
5
钙硫摩尔比钙硫摩尔比
5-13 SO2CaO
(Sar6%) 石灰石流量
0
5
10
15
20
25
02004006008001000
SO2排放
/mg.Nm3石灰石流量
/t.h-10
5
10
15
20
灰渣中平均CaO含量灰渣
CaO
含量
/%脱硫效率
90
92
94
96
98
100
02004006008001000
SO2排放
/mg.Nm3脱硫效率
/%0
1
2
3
4
5
钙硫摩尔比钙硫摩尔比
5-14 SO2CaO
(Sar=2%
Aar=50%
Qar,net=13MJ/kg)
第五章 CFB锅炉主要性能参数及结构尺寸的计算及选择
139
0.0
0.6
1.2
1.8
2.4
3.0
0.01.53.04.56.0
原煤含硫量 /%钙硫摩尔比中活性石灰石
低活性石灰石
高活性石灰石
(a) 0
25
50
75
100
0.01.53.04.56.0
原煤含硫量 /%脱硫效率
/%
(c) 石灰石流量
0
5
10
15
20
25
0.01.53.04.56.0
原煤含硫量 /%灰渣
CaO
含量
/%0
5
10
15
20
25
灰渣中平均CaO含量石灰石流量
/t.h-1
(b)
5-15 400mg/Nm3SO2Ca/S
CaO
(Sar=
2%Aar=25%Qar,net=22MJ/kg)
(a) 燃料含硫量与钙硫比Ca/S的关系
(b) 燃料含硫量与石灰石流量、灰渣中CaO含量的关
系
(c) 燃料含硫量和脱硫效率的关 从图中可以看出,为了得到相同的脱硫效率,燃料中的含硫量
S越低,则所需的Ca/S比
越高。这是因为含硫量越低,则烟气中的SO2浓度越低,因而反应所需的
Ca/S越高,才能达
到预期的脱硫效率。
另外,钙硫比Ks主要受石灰石活性
K、煤中含硫量S、所要求的脱硫效率εs和床温Tb等因素的影响。根据实际运行的数据,可以将钙硫比表达为:
Ks=
K1·K2·K3·K4 (5-61)
K1=2.17-0.965S+0.268S2-0.0352S3+0.00172S4 (5-62) K2=1.05exp[(
K-2)·0.25] (5-63) 234
3
56710311361289117372920
4777416385244121431ssss
sssK...
...
(5-64) 2
4348.0234100
1163
])1123(2)273()1123[(005.0
b
bbbT
TTTa (5-65) ]
)(25.1exp[12.02aab (5-66) )197.0/exp(4bc (5-67) 24.1/)]1(5[2
4
cck (5-68) 第五章 CFB锅炉主要性能参数及结构尺寸的计算及选择
140
式中
Ks——钙硫摩尔比;
S——燃料中硫含量,%;
εs——脱硫效率;
Tb——炉膛温度,
K。
表5-7为按式(5-61)对一些燃料的计算结果。 5-7
(5-61)
例1 例2 例3 例4 例5
燃料中硫含量 Sar,
%
1.93 0.5 1.46 3.12 1.66
要求的脱硫效率 εs,
%
92.3 84.5 91.0 94.5 94.3
炉膛温度 Tb,
K
1148 1156 1163 1170 1133
石灰石活性
K 中
优 中 优 中 优 中 优 中 优
需要的Ca/S比
Ca/S 2.5 1.9 3.46 2.63 2.69 2.04 2.06 1.77 2.67 2.3 表
5-8为几台大型CFB锅炉有关脱硫、NOx排放的设计数据。设计
数据是否准确还要经运行测试验证。 设计特性
里彦电厂
SG-465/13.7M
爱溪电厂
SG-220/9.9
新乡电厂
HG-440/13.7
晨鸣电厂
HG-220/9.8
石家庄电厂
DG410/9.81
保定电厂
DG450/9.81
威海电厂
UG220/5.3
Sar %
1.93 3.12 0.51 2.0 1.34 1.46 1.18
Nar %
1.27 0.71 1.14 0.81 0.98 0.91 0.75
Ca/S
2.2 1.75 2 2.2 2.3 2.3 2.1
石灰石耗量
kg/s
2.058 1.25 0.65 1.36 1.33 1.84 1.11
床层温度℃
875 893 883 874 896 896 898
炉膛出口温
度℃
875 893 883 874 882 884 889
NOx排放量
(O2=6%)
,
mg/m3(
标态)
202.8 250
≤150 ≤302
250 136 208
SO2排放量
(O2=6%)
,
mg/m3(
标态)
350 650
≤150 ≤294
250 400 454 5.2.23
Bsh
煤燃烧脱硫需加入的石灰石量:
Bsh=
B33
3CaCO
ars
caco
ars
CaCO125
.31SK
BSK
n
ns
,
t/h (5-69) 第五章 CFB锅炉主要性能参数及结构尺寸的计算及选择
141
式中
B——煤耗量,t/h;
nCaCO3——
碳酸钙的摩尔质量,kg/mol;
ns——
硫的摩尔质量,kg/mol;
εCaCO3——
碳酸钙在石灰石中的份额,%;
Ks——
钙硫摩尔比,Ca/s;
Sar——
燃料中所含的硫量,%。
5.2.24 Qpz
加石灰石脱时炉底排渣量Qpz的计算中,要知道如下参数:
煤耗量B kg/s;
石灰石耗量Bsh kg/s
;
煤中灰含量Aar %
;
排渣份额αpz %
。
由石灰石锻烧产生的灰渣量sh
pzQ可由式
(5-48)计算求得,为了简化计算,可取Ash=0.88Bsh,
再乘以αpz,即
=0.88Bshαpz,kg/s;
由煤中灰分产生的排渣量A
pzQ=
B·Aar·αpz,kg/s;
总的排渣量Qpz=sh
pzQ+ApzQ kg/s
例如,B=14.63 kg/s,Bsh=0.65 kg/s
,Aar =18.46 %,αpz =50 %,则
sh
pzQ=0.88
Bsh·αpz=0.88×0.65×0.5=0.285kg/s
A
pzQ=
B·Aar·αpz=14.63×0.1846×0.5=1.35kg/s
Qpz=sh
pzQ+ApzQ=0.285+1.35=1.635kg/s=5.89t/h
5.2.25 Qs
CFB锅炉燃烧的一个显著特点是在煤燃烧过程中加入石灰石实现脱硫。发生下述反应:
煅烧反应:
CaCO3→
CaO+CO2-183 kJ/mol (5-70)
固硫反应:
CaO+SO2+1/2O2→
CaSO4+ 486 kJ/mol (5-71)
煅烧与固硫反应的综合结果是输入热量有所增加,其增益量Qs:
第五章 CFB锅炉主要性能参数及结构尺寸的计算及选择
142
Qs=Sar·K
(152εs-57.19·βKs),kJ/kg (5-72)
式中 Sar——燃料中含硫量,
%;
K——SO2转化率,一般取
K =0.9;
εs——脱硫率;
β——煅烧率,取β=0.95~1;
Ks——钙硫摩尔比,
Ks=Ca/S,mol/mol。
加入石灰石后,燃烧所需空气量、烟气量、灰渣量等也有所增加,使q2、
q4、q6损失等有
所增加,具体增加量与Ca/S比大小及燃烧组织有关。
CFB的炉温下投入床内的全部石灰石均会生成CaO,而脱硫反应所产生的CaSO4与脱除
的SO2量有关。由于石灰的脱硫反应释出的热量大于石灰石煅烧反应所吸收的热量,因此最
后二者的平衡是增加了锅炉的热效率还是降低了锅炉的热效率,取决与脱硫所用的Ca/S(即石
灰石的流量),因为石灰的脱硫放热反应所释放的热量几乎是石灰石煅烧吸热反应所吸收的热
量的一倍,因此,Ca/S较低时,投入炉内的石灰石较少,石灰石煅烧吸热反应所吸收的热量
小于石灰的脱硫放热反应所释放的热量,因而总的效果是改善了锅炉效率。如果Ca/S较大,
则有可能使吸热大于放热,从而使锅炉效率降低。
对于三种不同的燃料,分别为含硫量为6%
的石油焦、含硫量为2%的煤和含硫量为2%的
煤矸石,在不同排放要求即脱硫效率不同时,
石灰石脱硫对锅炉效率的影响有所不同,见图
5-16。以石油焦为例,如果要求的排放值为
800mg/Nm3时,即脱硫效率为
92%,这时的锅
炉效率为93.2%。但如果要求的SO2排放值为400mg/Nm3,要求达到的脱硫效率为
96%,由于
提高了脱硫效率,导致Ca/S增加,使锅炉效率
略有下降,为92.7%,下降了0.5%。但是,即
使脱硫效率达到96%,加入石灰石脱硫实际上
也是提高了锅炉效率,见图5-17。
由图5-17可见,石灰石煅烧吸热反应对锅
炉效率的影响从SO2排放值
200mg/Nm3时的
-3%降至SO2排放浓度为
800mg/Nm3时的-2%。
而石灰的脱硫放热反应对锅炉效率的影响从
SO2排放值
200mg/Nm3至排放浓度为
800mg/Nm3时均为
+3%左右。因而,在SO2排88
90
92
94
96
02004006008001000
SO2排放
/mg.Nm3锅炉效率
/%石油焦
(6%S)煤(2%S)
矸石(2%S)
5-16
-4
-3
-2
-1
0
1
2
3
4
02004006008001000
SO2排放
/mg.Nm3锅炉效率
/%石灰石煅烧
白云石煅烧
硫酸盐化总影响
5-17 SO2(
) 第五章 CFB锅炉主要性能参数及结构尺寸的计算及选择
143
放值
200mg/Nm3时脱硫对锅炉效率没有影响,在SO2排放值800mg/Nm3时锅炉效率可增加约
0.7%。从图5-16和图5-17可以看出,在CFB中用石灰石脱硫对锅炉效率影响不大,其影响
随对SO2排放值的要求而不同,
SO2排放浓度越低,即Ca/S越高,它对锅炉效率的影响就越
大。一般说来,Ca/S≤2.5时,脱硫会增加锅炉效率;Ca/S>2.5时,脱硫会略降低锅炉效率。当
某些燃料如褐煤的灰分中CaO含量较高时,实际上添加的石灰石量可以较小,钙硫比较低,
则脱硫的热效应非常明显,此时脱硫利于改善锅炉效率,甚至可以提高锅炉效率达2~3%。
5.2.26 SO2
CFB锅炉石灰石脱硫并不是不能满足严格的SO2排放要求,很多锅炉的运行实践,已证
明了可以达到超过99%的脱硫效率。但是近年来对于气体排放的要求日益严格,仅仅脱除SOX,NOX和
CO到一定的水平已不够了,例如美国联邦法律要求,必须根据最佳的可用控制技术
((Best Available Control Technology 即ACT)逐步加强对空气污染物排放的处理。美国现在要新
批准的大型CFB锅炉项目,必须脱除所谓危险的空气污染物(Hazardous Air Pollutant 即HAPS)
如HCl、HFl、H2SO4和在火电厂排放的烟气中存在的其它酸性气体、飞灰中的微量元素,要
求新建的大型CFB锅炉要将烟气洗涤装置包括在锅炉系统中。因此目前美国三台在运行的容
量在250~300MWe的CFB锅炉安装了烟气洗涤装置。这就是美国一些电站CFB锅炉除了采
用石灰石炉内脱硫外,还在尾部空气预热器后面增设的第二级烟气脱硫系统,该系统包括一个
洗涤塔和一个袋式除尘器,其目的是除去CFB本身无法除去的酸性气体和微元素。这就是超
低排放SO2的
CFB锅炉。
将来自锅炉飞灰中的未反应的CaO随烟气进入一垂直布置的半干式反应塔,在反应塔中
通过喷水将飞灰中的CaO活化成氢氧化钙,或将新的水化石灰同时喷入反应塔,以进一步脱
除烟气中的SO2和酸性气体,与
HCl、HF和H2SO4进行反应。在烟气洗涤装置中,SO2和酸
性气体的脱除由两个分开的阶段进行。在第一个阶段,被喷入反应塔的雾化石灰浆液滴吸收。
在反应的同时在液滴中的水被蒸发掉,控制喷水量使吸收塔的出口温度保持在70~80oC
以上,
刚好超过烟气的绝热湿球饱和温度的20至30oC
。重金属(如汞Hg、铅Pb、钡Be等)先在反应
塔中凝结和收集,残存在烟气中的细微悬浮固体颗粒,随烟气和固体颗粒被导入一袋式除尘器
将固体颗粒除去。在第二阶段中,SO2和酸性气体和重金属等在烟气通过袋式除尘器的滤袋外
沉积的一层干灰层时被吸收。其效率主要取决于对细微颗粒(亚微米级)的过滤能力。颗粒收集
能力越强,脱除细微悬浮固体颗粒的效果越好。JEA的300WeCFB锅炉的反应塔可将90%的
汞脱除。如果需要,可将活性炭喷入袋式除尘器以进一步将汞除去。因此,袋式除尘器不仅可
非常有效地降低CFB锅炉的粉尘排放,而且对进一步降低烟气中的污染物也起着重要的作用。
降低锅炉酸性气体的排放要依靠反应塔,而去除微量元素则要靠袋式除尘器。通常,反应
塔除去HCl,HF,H2SO4的效率比脱除
SO2和的更高,也就是说,如果脱硫效率达到90%.时,
则脱除HCl、HF、H2SO4的效率可达
95%。
与单独的CFB锅炉相比,超低排放的CFB锅炉+烟气处理装置增加了设备投资和运行维第五章 CFB锅炉主要性能参数及结构尺寸的计算及选择
144
护费用,如用于洗涤塔的新石灰石、废物处理、水、电、运行维修的人工和材料等。如果考虑
NOX的超低排放,还需要考虑降低
NOX所需的氨消耗。
对酸性气体和微量元素的排放没有限值要求,CFB锅炉本身可满足严格的SO2排放要求,
在燃料含硫量>3%时,不应采用二级烟气反应塔方案。对于高硫燃料(>3%),在排放要求为
400mg/Nm3,此时要求的脱硫效率约为
97%。如果SO2排放限值所要求的脱硫效率要超过98
至99%,则需要进一步的研究是否需要采用反应塔。
若对酸性气体和微量元素的排放有限值要求,例如在美国,要求采用洗涤塔来控制酸性气
体,用袋式除尘器来控制微量元素的排放。这时,如果CFB锅炉本身脱除约80~92%的SO2,
而反应塔脱除另外的SO2,可以达到最佳的经济性。
5.2.27 NOx
各种燃烧方式的锅炉NOx最高排放浓度
(折算到烟气含氧量O2=6%时的干烟气NOx数值)
应符合GB13223所规定的排放限值。在没有NOx脱除装置时,燃烧过程中生产的
NOx量即为
排放的NOx量。
NOx生成浓度与燃烧工况及燃料含氮量有关,实测的NO及NO2体积浓度可
按下式换算为规定条件以NO2计算的质量浓度:
)]CC(05.2[
O21
621
C2xNONO
2
NO
(5-73)
式中 CNOx——在规定条件下
NOx的质量浓度,mg/m3(O2=6%);
C′NO——实测干烟气的
NO体积浓度,L/L;
C′NO2——实测干烟气的
NO2体积浓度,L/L;
O2——实测干烟气的含氧量,
%。
只测量NO的体积浓度C′NO时,可改用式
(5-74)计算: NO
2
NO
2
NOC
O21
4.32
C
95.0
05.2
O21
621
Cx
(5-74)
由于CFB锅炉较低的炉内燃烧温度以及分级送风,可有效抑制NOx的生成。研究表明,
燃烧温度低于1500℃时几乎观察不到高温型NOx的生成反应,因此
CFB锅炉中氮氧化物的生
成与控制重点是考虑燃料型NOx生成的控制。在通常煤的燃烧温度下,燃料型
NOx主要来自
挥发分N。所以高挥发分煤燃烧时NOx排放量要高于低挥发分煤排放量。当今运行的
CFB锅
炉运行温度在800~950℃,NOx排放量在
100~300 mg/m3(标态)范围内。我国2003年12月发布
的火电厂大气污染排放标准要求新建燃煤火电厂的NOx排放量,对于
Vdaf<10%的煤,烟气中
NOx排放
<1100 mg/m3(标态);对于10%≤Vdaf≤20%的煤,烟气中NOx排放650 mg/m3(标态);
对于Vdaf>20%
的煤,烟气中NOx排放<450 mg/m3(标态)。事实上,CFB锅炉的NOx排放量比
较低,远小于标准的规定。内江高坝电厂实际NOx的排放量仅为
64~78 mg/m3(标态)。 第五章 CFB锅炉主要性能参数及结构尺寸的计算及选择
145
5.2.28
Cfhq4
飞灰可燃物(又称飞灰含碳量)指飞灰中可燃物碳的质量占飞灰总量的比例。q4为固体未完
全燃烧损失的热量占锅炉总输入热量的比例。
影响q4的主要因素是煤质
(Vdaf、Aar、破碎粒度)、炉膛温度、风煤混合均匀性、分离器效
率、物料及飞灰在炉内的停留时间等。
对于同一种炉型的CFB锅炉,结构
参数差异不大,运行参数中炉温、二次
风供给方式等也变化不大,这种情况下,
煤质就成了影响燃尽程度的主要因素。
图5-18给出了若干台220 t/h及440 t/h
CFB锅炉燃用不同煤种得出的挥发分
Vdaf及燃料比
I与飞灰含碳量Cfh之间的
对应关系,即随着Vdaf减少,
Cfh相应增
加。一些100~135MWe级锅炉的性能考核试验数据示于表5-9。
5-9 100~135MWeCFB
项 目 济宁 运河 白杨河4#
白杨河5# 巡检司 杭热 香海 内江*
锅炉出力D
t/h 442 440 416 422 440 213 220 410
煤质
Vdaf
% 38.7 41.28 18.34 20.9 52.7 32.6 35.24 17.9
Aar
% 23.39 27.85 34.38 32.45 11.45 30.59 28.8 25.59
Qnet,ar
MJ/kg 22.2 19.95 19.94 20.49 12.44 21.8 20.83 22.59
飞灰含碳量Cf
h
% 6.59/7.85 7.41 13.8 12.85 4.74 7.05 7.04 18.78
底渣含碳量Clz
% 0.89 0.98 1.24 1.17 0.8 2 1.11 4.3
未燃碳损失q4
% 1.69 1.29 5.3 4.45 2.2 3.3 2.48 5.16
排烟温度t排
℃
- 160 147 134.9 149 169.5 168 135
下床温度t下床
℃
- 833~845 887 901 865 832 864 -
锅炉效率ε
% 91.45 91.29 90.57 91.2 91.39 89.53 89.73 89.59
飞灰底渣比af
h/alz
51/49 - 40/60 40/60 62.5/37.5 79/21 65/35 31/69
石灰石系统
投 投 投 投 没投 投 没投 投
数据来源
性能验收 性能验收 性能验收 性能验收 运行数据 性能验收 性能验收 性能验收
测试单位
热工院 山东院 热工院 热工院 哈锅 浙大 辽宁院
热工院 从表中数据看出,其
Cfh与Vdaf的关系与图5-18给出的关系相当符合。由此,图5-18给
出的曲线可以作为CFB锅炉不同煤种选择Cfh和
q4的参考。在锅炉设计时,应该尽量采取其
他有利于减少Cfh的措施,如提高炉膛温度,加强风煤的混合,增加飞灰在炉内的停留时间等
如飞灰再循环,内江410 t/h锅炉改造飞灰再循环后Cfh由
18.78%降至13%。
5-18 220 t/h440t/h CFBICfh 第五章 CFB锅炉主要性能参数及结构尺寸的计算及选择
146
注:燃料比的计算举例:
例如某煤的Vdaf=15%
,即表示每公斤煤中有150 g挥发分,Qnet,ar=25.5 MJ/kg,即表示每公斤煤中有25.5 MJ
发热量,由此I= Vdaf/
Qnet,ar=150 g/25.5 MJ=5.88 g/MJ。 锅炉热效率测定中,固体未完全燃烧热损失按式(5-75)计算: ]
C-100
C
C-100
C
[
100
107.33lz
lz
lz
fh
fh
fh
arv,net,
shar
3
4
Q
AA
q (5-75)
式中 q4——固体未完全燃烧热损失,
%;
33.7×103——灰中含碳的近似发热量,
kJ/kg;
Aar——入炉煤收到基灰分,
%;
Ash——加石灰石脱硫增加的灰分,
kg/kg(煤),见式(5-48);
Qnet,v,ar——入炉煤收到基低位发热量,
kJ/kg;
Cfh、
Clz——飞灰和炉渣中的含碳量,%;
afh、
alz——飞灰和炉渣中的灰分份额。它们之间的关系为:afh+alz=1。
5.2.29 DminBMLR
最低不投油负荷Dmin指在设计煤种和合同规定条件下无油助燃所能达到的最低稳定运行
锅炉负荷。最低不投油稳燃负荷率BMLR指最低不投油负荷Dmin与锅炉最大连续负荷
BMCR
之比。
由于CFB锅炉密相区床层具有较高的热容量,故使锅炉具有很好的燃烧稳定性和低负荷
稳定性。影响Dmin的主要因素是燃料特性
(挥发份含量)和床层温度。对于低Vdaf煤应采取较高
的床温。在谈到最低不投油负荷时应注意到,每台锅炉都具有3个不同定义的最低不投油负荷:
即设计保证值、试验值和可供调度值。试验值是在设计煤种及正常工况条件下经持续4~6小
时稳定运行试验可达到的最低数值,而电厂在日常运行时考虑意外情况,为保持安全运行所采
用的Dmin值要高于试验所能达到的最低值,称为可供调度值。设计保证值是锅炉制造厂保证
的Dmin数值,取锅炉最低不投油负荷试验值,一般为
30%最大连续负荷。 5.3 5.3.1 Flt
炉膛横截面面积由BMCR负荷时的空截面烟气速度Wx决定,见式
(5-21)。一旦烟气速度
决定,则截面积F就已决定: p
W
VB
F
325.101
273
273pj
x
yj
lt
,m2 (5-76) 第五章 CFB锅炉主要性能参数及结构尺寸的计算及选择
147
5.3.2
(b)(a)b/a
b/a比的确定要考虑二次风在炉膛内有足够的穿透深度,便于燃料、石灰石及回料的供给
与扩散,同时考虑炉膛内受热面与尾部受热面布置、分离器的布置等相协调等。炉膛的深度a
一般不宜大于8m。若锅炉容量很大,需要增大深度时,可在炉膛下部采取裤衩结构。
5.3.3 FBF
为了确保流化质量,锅炉在低负荷时也能维持良好的床内流化质量,通常布风板的面积设
计得较小,并采取向上渐扩的结构,以防止底部粗颗粒的沉积,减少床料分层和结渣的可能性。
布风板的截面积由密相区空截面风速Wm确定,见式
(5-18)。风速确定后即可求出布风板
截面积FBF:
PW
aVBr
F
325.101
273
273pj
m
0
j1
BF
,m2 (5-77)
对于等流速变截面设计的炉膛布风板面积的确定还有一种方法,即 1
lt
BFr
F
F
一次风率
炉膛截面积
布风板面积
(5-78)
由式(5-78)可知,炉膛截面积Flt和一次风率
r1确定后,即可求出布风板截面积FBF。例如
一次风率取为0.5,则布风板面积即为炉膛截面积的一半。
布风板的宽度一般与炉膛宽度相等,由此可求出布风板的深度。通常布风板的深度不应超
过3.7~3.8 m,过宽则布风均匀性难以保证,为此大型CFB锅炉通常采用裤衩腿结构。
5.3.4 h2
炉膛高度的确定要考虑以下因素:
① 将烟气冷却到需要的炉膛出口烟气温度;
② 保证分离器不能捕集的细粉在炉内一次通过时能够燃尽;
③ 应容纳炉内布置的蒸发及过热、再热器受热面;
④ 保证回料器料腿一侧有足够的静压头,以保证物料的循环;
⑤ 保证脱硫所需最短的停留时间。
对于大容量CFB锅炉来说,在上述各项中第①、②项是主要的,并兼顾尾部烟道的高度
要求,一般根据经验选取,表5-10给出从布风板至炉顶全高度的推荐参考值。对于较小容量
的流化床锅炉而言,可能由于炉膛较高而过热器受热面过多,因此应该在合适的位置上设置卫
燃带;对于较大容量的流化床锅炉,由于炉膛水冷壁面积相对于容量而言较小,因此需要在燃
烧室上部布置受热面,如双面受热水冷屏、隔墙水冷壁、过热器翼形墙、再热器翼形墙等。这
些炉内受热面的数量应根据传热计算确定。对于300MWe以上的亚临界或超临界,炉膛上部
无法布置太多的受热面,而需要设置流化床换热器,流化床换热器中受热面的多少,也要根据第五章 CFB锅炉主要性能参数及结构尺寸的计算及选择
148
传热计算确定。
5-10 (m)
项目
锅炉容量 t/h
35 75 130 220 410 670 980 1996
煤种
无烟煤
18 22 28 33 37 44 53 64
贫煤
16 21 26 31 35 42 51 61
烟煤
15 20 25 29 33 39 49 56
褐煤
14 18 24 28 30 37 47 51 5.3.5
下排二次风口的位置是密相区与过渡区的分界,也就决定了密相区的高度。密相区高度对
燃料的燃烧、锅炉运行(特别是变负荷)的稳定性以及一次风机的电耗均有影响,需综合考虑而
定。早期的循环床锅炉密相区高度(从布风板到二次风口)达6m,目前都趋于降低,通常取密
相区高度(即从布风板到下二次风口位置)为1~2m。而整个过渡区(最下排二次风口到最上排二
次风口)的距离为2~4m。
二次风沿炉膛高度的布置层数一般为2层。也有3层的。层数多似乎混合均匀,但是风量
分散,动量降低,影响穿透深度,因此应综合考虑。
5.3.6
(1) 给煤口
在给煤口,燃料主要通过重力给入循环流化床内,为了防止高温气体从炉内通过给煤口反
吹,要求给煤口压力高于炉膛压力,通常是将进料口和上部的给料装置密封。给料点一般布置
在敷设有耐火材料的炉膛下部还原区,并且尽可能地远离二次风入口点,从而使细煤颗粒在被
高速气流夹带前有尽可能长的停留时间。在有些锅炉中煤首先被送入返料机构,在进入循环流
化床锅炉炉膛前进行预热,这特别适合于高水分和粘结性强的燃料。由于煤仓间通常布置在锅
炉前部,后墙回料阀给煤一般要采用三级给煤,给煤系统复杂。由于给煤经过的环节比较多,
特别是刮板输送机的机械设备维护量较大,影响了机组的可靠性。这一系统中,由于给煤进入
回料管处是正压,因此给煤系统均处于正压。发生下煤管堵煤时,正压使得疏通非常困难。为
了提高给煤的可靠性,应该合理降低给煤系统的复杂性。如果采用前墙给煤,可以大大简化,
采用一级给煤即可。实践表明,返料阀中回灰管给煤改为前墙给煤,对燃烧的影响非常小。
有关给煤口的个数,可以根据扩散理论进行计算来确定单位横截面积所需的给料点数。但
由于循环流化床的横向混合比鼓泡流化床强烈,所以其给煤点可以比鼓泡流化床锅炉少。
(2) 石灰石给料口
石灰石由于其反应速率比煤燃烧速率低得多,而且石灰石给料量少,粒度又较小,所以其
给料点的位置及个数不象给煤点那么关键,石灰石可以采用气力输送单独送入床内,也可以将第五章 CFB锅炉主要性能参数及结构尺寸的计算及选择
149
其送入循环物料口或给煤口给入。
(3) 床层底部排渣口
循环流化床底部的排渣口主要用于床层的最底部排放床料。它的主要作用有二:第一是维
持床内固体颗粒存料量;第二是维持颗粒尺寸,不使过大的颗粒聚集于床层底部而影响循环流
化床锅炉的运行。
排渣管应布置在床层的最低点,一般可采用两种布置方式:一种是布置在布风板上,即取
消一定数量的风帽,而代之以排渣管。排渣管的尺寸应足够大以使大颗粒物料能顺利地通过排
渣管排出;第二种方式是将排渣管布置于炉壁靠近布风板处,这样就不需要在布风板上开孔布
置排渣管,且便于冷渣器的布置。但在床面较大时,这种形式就比较难布置。
排渣口的个数应视燃料颗粒尺寸而定。当燃料颗粒尺寸较小,且比较均匀时,可采用较少
的排渣口,但如果燃用的燃料颗粒尺寸较大应增加排渣口,使可能沉底的大粒渣及时排出。 5.4
锅炉的结构尺寸基本上是按满负荷时选取的,在低负荷运行时需要根据燃烧的要求进行调
整,一般当锅炉负荷降到50%~60%额定负荷时蒸汽参数可以维持额定设计值,低于这个负荷
时蒸汽温度和压力都要有所降低。炉内的一些性能参数也都要发生不同的变化。
5.4.1
在负荷降低时床温及炉膛出口温度都将随着降低,尤其炉出口温度(由于循环流率的降低)
降低更快。假定满负荷时床温与炉出口温度相等,则低负荷时可参考表5-11,其主要影响因
素是风速和烟速、循环物料尺寸及物料量(床层厚度)等。 5-11
锅炉负荷,%
100 75 50
床温℃
850~880 835~865 810~835
炉膛出口温度℃
850~880 820~845 735~760 5.4.2
当负荷降低时循环流量降低,在床存量不变的情况下,床层厚度增加,床压因而升高。
当给煤量与一次风量维持不变,通过减少排渣量而增加床压(床层高度)的时候,由于床层
阻力的增加影响燃烧速率而使床温降低;反之,当增加排渣量而减低床压时床温升高。
5.4.3
低负荷时循环流化床向鼓泡床过渡。在低负荷下,总风量下降,为了维持良好的流化,一
次风量不能低于初始流态化所需要的风速,因此一次风率随负荷的降低而增加。内江高坝电厂
燃用贫煤的410 t/h CFB锅炉负荷变化特性试验结果如图5-19~5-14。 第五章 CFB锅炉主要性能参数及结构尺寸的计算及选择
150
5-19
5-20 5-21 5-22 5-23 5-24 可以看出,该炉在100%~30%负荷范围内,主蒸汽压力随负荷减少而降低,而汽温变化随
负荷变化量较小,变化范围为535~525℃,锅炉的这一汽温特性主要是由于采用了辐射对流过
热器串联布置,因而在负荷变化时具有较平稳的汽温特性。在30%~100%负荷范围内,Ⅰ、Ⅱ
级减温水流量均较小,总减温水流量<4.2 kg/s (15.12 t/h),为额定蒸发量的3.6%,和设计值6.3
kg/s(为锅炉额定蒸发量的5.5%)较为接近。当负荷变化时,锅炉的一次风率在60.9%~83.5%范
围内变化,随着负荷减少,一次风率增大,二次风率减少。炉膛下部床温变化范围为902~764℃,
负荷降低,床温亦降低。炉膛出口温度随锅炉负荷减少而下降,100%~30%负荷下,在880~678℃
变化。锅炉在30%~100%负荷下运行时,炉膛下部和炉膛出口之间存在一定的温差,此温差大第五章 CFB锅炉主要性能参数及结构尺寸的计算及选择
151
小随负荷而变化,基本的变化趋势是锅炉蒸发量增大,炉膛上下温差减少,其变化范围为
102~7.75℃。该炉升负荷过程中的各参数变化见图5-25。 5-25
410 t/h CFB 宁波中华纸业公司220 t/h CFB锅炉曾做过负荷变化特性试验,结果见图5-26。从图中看
出,其变化规律与高坝410 t/h炉相似。 第五章 CFB锅炉主要性能参数及结构尺寸的计算及选择
152
5-26
该炉在100%~30% MCR范围内,主蒸汽压力随负荷减小而降低,主汽温度随负荷的减小
也减小,但变化量较小,变化范围为
546~521℃,具有较平稳的汽温特性;炉膛下部床温随负
荷的降低而降低,床温的变化范围为
864~796℃;炉膛出口烟温随负荷的降低而降低,温度变
化范围为875~632℃;炉膛下部和炉膛出口之间存在一定的温差,基本趋势是锅炉蒸发量增大,
炉膛上下温差减小,变化范围为164~11℃;一次风率变化趋势是锅炉负荷降低一次风率增加,
变化范围为随锅炉100%~30%额定负荷为61.69%~94.69%。 第五章 CFB锅炉主要性能参数及结构尺寸的计算及选择
153
5.4.4
αfh
随负荷降低,烟气速度降低,分离器效率降低,故飞灰份额略有增加。
5.4.5
随负荷降低,一次风量减少,风速降低,但由于低负荷时一次风率增加,故其风速降低的
份额小于负荷降低的份额。
5.4.6
随负荷降低烟速降低。由于低负荷时过剩空气量大于额定负荷时(50%负荷时α取为1.5),
故烟速降低的份额略小于负荷降低的份额。如某台135 MWe贫煤炉,100%负荷时烟速为
5.7m/s,而50%负荷时烟速为3.2 m/s。
5.4.7
随着负荷的降低,分离器效率降低,循环倍率降低,循环流率降低,物料浓度降低,传热
系数也降低。
5.4.8
由于烟速降低,故低负荷时一次性通过炉膛的物料在炉内的停留时间增长,故在负荷不高
时飞灰可燃物减少,但由于炉内温度水平降低,在负荷降低到70%以下时飞灰可燃物增加,
q4增加。
5.4.9
随着循环流率的降低,密相区燃烧份额增加。这在某种程度上减缓了床温的降低,对低负
荷燃烧稳定性有利。
5.4.10
低负荷时过热器喷水量占锅炉总
蒸发量的份额增加。如某台135 MWe
锅炉满负荷时喷水量占锅炉总蒸发量
的份额为4.15%,共18.21t/h,则50%
负荷时为8.19%,共15.91 t/h。从总体
上看,随着负荷的降低,喷水量下降。
5.4.11
随着负荷的降低,机组热耗增加,
厂用电率增加,见图5-27。 5
-27 第五章 CFB锅炉主要性能参数及结构尺寸的计算及选择
154
5.5
锅炉设计性能保证值是制造厂向锅炉用户的产品性能承诺,是考核设计质量的依据,体现
性能设计参数选择的正确性,体现锅炉设计的水平,是研究分析性能参数及结构尺寸的最终目
的。性能保证值通过考核试验来确认。设计者应根据用户提供的锅炉容量、燃用煤质及要求的
性能保证内容等设计条件选定性能保证的数值。
性能保证的范围主要包括:
① 锅炉铭牌(最大连续)出力及设计参数(出口蒸汽压力、温度);
② 锅炉效率;
③ 无油助燃最低稳定运行负荷;
④ 过、再热器喷水量;
⑤ 脱硫效率及SO2、
NOx排放浓度。
5.5.1 ()
从已投运的50 MWe以上容量锅炉运行结果看,只要保证分离器的分离效率均能达到最
大连续出力及相关的蒸汽参数(温度和压力值)。
5.5.2 η
锅炉效率ε用反平衡方法求取。 6
54321qqqqq,% (5-79)
式中 q2——排烟热损失,
%;
q3——可燃气体未完全燃烧热损失,
%;
q4——固体未完全燃烧热损失,
%;
q5——散热损失,
%;
q6——排渣热损失,
%。
(1) q4的选取
锅炉效率与燃用的煤种挥发分、灰分、发热量、破碎粒度及炉膛温度、风煤混合均匀性、
分离器效率、物料及飞灰在炉内的停留时间等有关。在锅炉设计时应参考已经投运的同煤种锅
炉实际效率选取值。当煤种有变化及没有燃用过的煤种可参考图
5-8确定飞灰可燃物Cfh并
按式(5-75)计算q4值。图
5-18给出的是按燃料比(干燥无灰基挥发分与煤的低位发热值之比)
所得的飞灰可燃物Cfh含量。该图是根据若干台实际运行的锅炉飞灰可燃物
Cfh绘制的,图中
中线以下是最理想的情况,特别是对于低挥发分的贫煤、无烟煤较难达到,而一般是中线范围。
当按图和公式计算所得的Cfh和
q4值满足不了用户的要求时,应采取特别的提高燃尽率的措施,第五章 CFB锅炉主要性能参数及结构尺寸的计算及选择
155
如改善破碎粒度、提高炉膛温度、加强风煤混合以及采用飞灰再循环等措施。
一般q4损失在下列范围:
贫煤、无烟煤:q4=3%~6%
;
烟煤:q4=1.5%~3%
;
褐煤:q4=0.6%~1.5%
。
(2) 排烟热损失q2
排烟热损失大小决定于燃料完全燃烧产生的烟气量和排烟温度。一般贫煤、无烟煤的烟气
量小于烟煤,低约5 %~6 %;褐煤的烟气量高于烟煤,高约8%~9%。对于含硫量高的燃料,
排烟温度要选取高值,一般当Sar>1.0
时,取py=130~140℃;Sar小于1.0时取py≈130℃。
一般排烟温度提高10℃时q2约增加
1%,故对于低挥发分燃料,为了弥补q4损失的增高,应
尽量降低排烟温度。为了降低排烟热损失,应减少系统漏风,尾部烟道应装设有效的吹灰装置。
一般排烟热损失在下列范围:
贫煤、无烟煤:q2=4.5%~5.5%
;
烟煤:q2=5.5%~6.0%
;
褐煤:q2=6.0%~6.8%
。
(3) 排渣热损失q6
排渣热损失主要决定于排渣量Mpz与排渣温度
pz。
排渣量大小决定于燃料灰分含量和脱硫用的石灰石耗量。特别是对于矸石含量高的燃料
q6损失最大。排渣温度一般取
<150℃。当冷渣器运行性能较差时排渣温度要升高。q6损失一
般在0.1%~1.0%范围内,对于矸石含量大的煤q6可达
1.4%以上。
(4) 锅炉效率的计算
锅炉效率的计算一般用反平衡法。前段时间国内计算主要采用美国ASME PTC4.1规程计
算,最近西安热工院编写了中国循环流化床性能试验规程,正在征求意见过程中。通过后按新
的规程执行。现将ASME PTC4.1规程的计算实例列于表5-12,供参考。 5-12 CFB
(ASME PTC4.1)
项 目 符号 单位 数据来源 褐煤 贫煤
一.试验煤质资料
收到基碳
Car
%
化验值
36.72 48.58
收到基氢
Har
%
化验值
1.87 2.57
收到基氧
Oar
%
化验值
12.59 2.54
收到基氮
Nar
%
化验值
1.01 0.96
收到基硫
Sar
%
化验值
1.66 2.47
第五章 CFB锅炉主要性能参数及结构尺寸的计算及选择
156
5-12 CFB(ASME PTC4.1)
全水分
Mar
%
化验值
34.70 6.80
收到基灰分
Aar
%
化验值
11.45 36.08
收到基高位发热量
HHV kJ/kg
化验值
13730 19402
收到基低位发热量
HLV kJ/kg
化验值
12435 18650
实际燃料消耗量
B kg/s
记测值
28.69 21.020
二.试验石灰石成分
碳酸钙
CaCO3
%
化验值
97.40 97.50
碳酸镁
MgCO3
%
化验值
1.00 1.932
水分
Ms
%
化验值
0.23 0.00
其它
As
%
化验值
1.32 0.0076
实际石灰石耗量
G kg/s
记测值
2.340 3.450
三.钙硫摩尔比
SO2转换率
k %
按90取定
90.0 90.0
钙硫摩尔比
Ca/S 32×CaCO3×
G/(100×B×k/100×Sar) 1.70 2.30
四.灰渣量
脱硫效率(假设值) s
%
先假定90,再循环计算。
90.13 90.13
脱硫效率(计算值) s
% 90.13 90.11
CaSO4生成量
ACaSO
4
kg/kg煤
4.246×s/100×Sar×k/100 5.72 8.51
未反应的氧化钙
ACaO
kg/kg 1.75×k/100×Sar×[(Ca/S)-s/100] 2.09 5.46
石灰石中杂质量
A´ kg/kg 3.125×(1-CaCO3/100
-Ms/100)×k/100×Sar×Ca/S 0.0019 0.0040
灰渣量
A kg/kg Aar+
ACaSO4+ACaO+A´ 19.26 50.05
五.灰渣可燃物
飞灰比率
rf
%
待定(47%)
62.5 51.0
炉渣比率
rs
%
待定(53%)
37.5 49.0
沉降灰比率
%
飞灰可燃物
Cf
%
化验值
5.88 6.00
炉渣可燃物
Cs
%
化验值
0.80 1.00
沉降灰可燃物
%
灰渣平均可燃物
Cav
% rs×Cs/100+rf×Cf/100 3.98 3.55
干灰渣量
Wdp
kg/kg
A×100/(100-Cav)
20.06 51.89
实际烧掉的碳
Cb
kg/kg Car-Wdp×Cav/100 35.92 46.74
六.烟气特性
预热器出口氧量
O2
%
实测值
3.2 3.5
预热器出口CO2
CO2
%
实测值
17.4 16.0
预热器出口CO
CO %
实测值
0.0010 0.0010
第五章 CFB锅炉主要性能参数及结构尺寸的计算及选择
157
5-12 CFB(ASME PTC4.1)
排烟中so2浓度
CSO
2" L/L
实测值
260 270
预热器出口氮
N2
% 100-O2-CO2-CO 79.4 80.5
理论空气量 A´θ
kg/kg
[11.51Ca
r+34.30×(Har-Oar/7.937)+4.335×Sar +2.159×Sar×s/100]/100
4.428 6.518
预热器出口干烟气量
WG´
kg/kg
[(44.01×CO2+28.01×CO+32.00×O2+28.02×N2)/
12.01/(CO2+CO)
]×[Cb+12.01/32.07×Sar×k/100×
(1-s/100)+(Ca/S)×12.01/32.07×Sar×
k/100]/100
5.466 7.790
预热器出口干空气量
WA´
kg/kg
{28.02×N2×
[Cb+12.01/32.07×Sar×k/100×
(1-s/100)+Ca/S×12.01/32.07×Sar×
k/100]/12.01
/(CO2+CO)
-Nar}/0.7685/100
5.102 7.431
干烟气密度 γ
kg/m3
0.04299×(CO2/35.11+O2/48.28+N2/55.14+
CO/55.16)×16.018
1.378 1.369
七.脱硫效率
SO2生成量
SO2
´
kg/kg煤
64.07/32.07×k/100×Sar/100 0.03 0.04
计算二氧化硫浓度
CSO
2´ mg/m3
SO2´/
WG´×γ×1000000×[15/(21-O2)]
6344 6690
排烟中SO2浓度
CSO2
mg/m3
CSO2"×15
/(21-O2)×64.07/22.41
626 662
脱硫效率 s
%
(1-CSO2/
CSO2´)×100
90.13 90.11
八.大气条件
大气压力
PA
kPa
实测
88.40 101.28
干球温度
td
℃ 实测
20.0 20.0
湿球温度
tw
℃ 实测
17.0 17.0
相对湿度 φ
%
查表
71.0 80.0
饱和蒸汽压力
Pb
Pa
611.7927+42.7809×td+1.6883×
td
2+
1.2079/100×td
3+6.1637/10000×
td
4
2338 2338
空气含湿量
WmA´
kg/kg
0.622×φ/100×Pb/(1000×
PA-φ/100×Pb)
0.012 0.012
九.基准温度
一次风量
Wp
kg/s
实测
261.5 261.5
二次风量
Ws
kg/s
实测
230.0 230.0
预热器进口一次风温
tp
℃ 实测
20.0 20.0
预热器进口二次风温
ts
℃ 实测
20.0 20.0
基准温度
tRA
℃
(tp*Wp+tsWs)/(Wp+Ws) 20.0 20.0
烟气中水分
mG
kg/kg 8.936×Har/100+WmA×WA´+Mar/100+Ms/100×G/B 0.58 0.38
排烟温度 "py
℃ 实测值
149.0 138.0
渣温
tlz
℃ 实测值
150.0 150.0
烟气中水分分压力
PmG
Pa 1000×PA/{1+150×Cb/100/[mG×(CO2+CO)]} 13845 8173
烟气中水蒸汽焓
h" kJ/kg
查表(根据"py,
PmG)或计算
2782.8 2761.7
第五章 CFB锅炉主要性能参数及结构尺寸的计算及选择
158
5-12 CFB(ASME PTC4.1)
饱和水蒸汽焓
hRV
kJ/kg
查表(根据tRA)
或计算
2538.2 2538.2
CO
干烟气平均比热
CpG´
kJ/(kg℃) 查图(根据"py,
tRA)
1.0083 1.0091
炉渣比热
Cplz
kJ/(kg℃)
0.79 0.79
飞灰比热
Cpfh
kJ/(kg℃)
0.78 0.78
十.锅炉效率计算
未燃碳分热损失
Luc
% 33722×Wdp/100×Cav/HLV 2.16 3.33
干烟气带走的热损失
LG
% 100×WG´×CpG´×("py-tRA)/HLV 5.717 4.974
燃料水分热损失
Lmf
% Mar×(h"-hRV)/HLV 0.68 0.08
氢生成的水的热损失
LH
% 8.936×Har×(h"-hRV)/HLV 0.33 0.28
空气中湿分的热损失
LmA
% 100×WmA´×WA´×(h"-hRV)/HLV 0.12 0.10
石灰石中水分热损失
Ls
% Ms×G/B×(h"-hRV)/HLV 0.0004 0.0000
CO引起的热损失
LCO
% 23632×Cb×CO/(CO2+CO)/HLV 0.0039 0.0037
辐射对流热损失
LR
%
查图
0.34 0.28
灰渣显热损失
Ld
%
Wdp×
[Cpfh*rf/100×("py-tRA)+Cplz*rs/100
×(tlz-
tRA)]/ HLV
0.1638 0.2697
CaCO3煅烧热损失
LCaCO
3 % CaCO3×G/B×1830/HLV 1.17 1.57
硫酸盐化放热
q % Sar×k/100×s/100×15141/HLV
1.64 1.63
总热损失
L % Luc+
LG+Lmf+LH+LmA+Ls+LCO+LR+Ld+LCaCO3-q 9.05 9.26
锅炉效率
% 100-L 90.95 90.74
十一.效率修正
1.煤质资料
收到基碳
Cd
%
设计值
36.72 48.58
收到基氢
Hd
%
设计值
1.87 2.57
收到基氧
Od
%
设计值
12.59 2.54
收到基氮
Nd
%
设计值
1.01 0.96
收到基硫
Sd
%
设计值
1.66 2.47
全水分
Md
%
设计值
34.70 6.80
收到基灰分
Ad
%
设计值
11.45 36.08
收到基高位发热量
HHVd
kJ/kg
设计值
13730 19402
收到基低位发热量
HLVd
kJ/kg
设计值
12435 18650
设计燃料消耗量
Bd
kg/s
设计值
28.690 21.020
第五章 CFB锅炉主要性能参数及结构尺寸的计算及选择
159
5-12 CFB(ASME PTC4.1)
2.设计石灰石成分
碳酸钙
[CaCO3]d
%
设计值
97.40 97.50
碳酸镁
[MgCO3]d
%
设计值
1.00 1.932
水分
Msd
%
设计值
0.23 0.00
其它
Asd
%
设计值
1.32 0.0076
设计石灰石耗量
Gd
kg/s
设计值
2.340 3.450
3.脱硫效率
SO2转换率
k %
按90取定
90.0 90.0
钙硫摩尔比
(Ca/S)d
设计值
1.70 2.30
脱硫效率 s
%
计算值
90.13 90.11
4.灰渣量
CaSO4生成量
(ACaSO
4)d
kg/kg煤
4.246×s/100×Sd×k/100 5.72 8.51
未反应的氧化钙
(ACaO)d
kg/kg 1.75×k/100×Sd×[(Ca/S)d-s/100] 2.09 5.44
石灰石中杂质量
A´d
kg/kg
3.125×(1-[CaCO3]d/
100-Msd/100)×k/100
×Sd×(Ca/S)d
0.19 0.40
灰渣量
A° kg/kg Ad+(
ACaSO4)d+(ACaO)d+A´d 19.44 50.43
5.灰渣可燃物
灰渣平均可燃物
Cav°
% rs×Cs/100+rf×Cf/100 3.98 3.55
干灰渣量
Wdpd
kg/kg A°×100/(100-Cav°) 20.25 52.28
实际烧掉的碳
Cbd
kg/kg Cd-Wdpd×Cav°/100 35.92 46.72
6.空气、烟气特性
预热器出口干烟气量
WG´d
kg/kg
[(44.01×CO2+28.01×CO+32.00×O2+28.02×N2)
/12.01/(CO2+CO)
]×[Cbd+12.01/32.07×Sd×k/100
×(1-s/100)+(Ca/S)d×12.01/32.07×Sd×
k/100]/100
5.464 7.788
预热器出口干空气量
WA´d
kg/kg
{28.02×N2×
[Cbd+12.01/32.07×Sd×k/100
×(1-s/100)+(Ca/S)d×12.01/32.07×Sd×
k/100]
/12.01/(CO2+CO)
-Nd}/0.7685/100
5.101 7.429
设计空气含湿量
WmA´d
kg/kg
设计值
0.012 0.012
保证基准温度
tRAd
℃ 设计值
20.0 20.0
预热器进口烟温 ´
℃ 实测值
279.0 299.0
修正后的排烟温度 "d
℃
[tRAd×(´-"py)+ ´×("py-tRA)]/( ´-tRA) 149.0 138.0
烟气中水蒸汽焓
h"d
kJ/kg
查表(根据"d,
PmG)或计算
2781.5 2760.4
饱和水蒸汽焓
hRVd
kJ/kg
查表(根据tRAd)
或计算
2538.2 2538.2
CO
第五章 CFB锅炉主要性能参数及结构尺寸的计算及选择
160
5-12 CFB(ASME PTC4.1)
干烟气平均比热
CpG´d
kJ/(kg℃) 查图(根据"d,
tRAd)
1.0083 1.0091
7.修正后的锅炉效率
干烟气带走的热损失
LGd
% 100×WG´d×CpG´d×("d-tRAd)/HLVd 5.7155 4.9721
燃料中水分热损失
Lmfd
% Md×(h"d-hRVd)/HLVd 0.68 0.08
氢生成的水分热损失
LHd
% 8.936×Hd×(h"d-hRVd)/HLVd 0.33 0.27
空气中湿分的热损失
LmAd
% 100×WmA´d×WA´d×(h"d-hRVd)/HLVd 0.12 0.11
石灰石中水分热损失
Lsd
% Msd×Gd/Bd×(h"d-hRVd)/HLVd 0.0004 0.0000
石灰石煅烧热损失
L(
CaCO3)d %
设计值
1.17 1.57
硫酸盐化放热
qd
%
设计值
1.64 1.63
修正后总热损失
Lt
%
Luc+
LGd+Lmfd+LHd+LmAd+Lsd+LCO+
LR+
Ld+L(CaCO3)d-qd
9.0394 9.2570
修正后的锅炉效率 d
% 100-Lt 90.96 90.74
修正的未燃碳热损失
Lucd
% Luc*HLV/HLVd 2.16 3.33
修正后的锅炉效率 d
%
100-Lucd+
LGd+Lmfd+LHd+LmAd+Lsd+LCO+
LR+
Ld+L(CaCO3)d-qd
90.96 90.74
**试验燃料比设计燃料差时考虑该项修正才有利。
5.5.3 BMLR
锅炉最低不投油稳燃负荷率的定义是在设计煤种和合同规定条件下,锅炉不投油助燃的最
低稳定燃烧负荷与锅炉最大连续负荷(BMCR)之比。
锅炉最低不投油稳燃负荷率(BMLR)的计算式如下: %
100
BMCR
负荷不投油助燃的最低稳投
BMLR (5-80)
每台煤粉锅炉都可能具有3个不同定义的最低不投油稳燃负荷率数值,即:
——设计保证值:锅炉制造厂保证的数值;
——试验值:在设计煤种及正常工况下经持续4~6 h稳定运行(无局部灭火及炉膛负压大
幅度波动现象)试验可达到的最低数值;
——可供调度值:考虑到日常入炉煤质波动及设备状态和控制水平、火焰检测系统的可靠
性等条件后由业主规定的可供负荷调度用的实际运行数值。
在锅炉设计时一般以最低不投油负荷率试验值作为锅炉最低不投油稳燃负荷率。 锅炉最低不投油稳燃负荷率与燃用的煤种
(Vdaf,Qnet,ar)、密相区的床层温度及热容量有关。
从已投运的锅炉测试结果看,贫煤锅炉均可以达到最低不投油稳燃负荷率试验值,为30%,
而实际可供调度值要大于30%。 第五章 CFB锅炉主要性能参数及结构尺寸的计算及选择
161
对于烟煤锅炉可取
BMLR试验值为28%~30%,对于无烟煤锅炉可取BMLR试验值为
35%~45%。
为了降低最低不投油稳燃负荷率,在不产生结渣情况下应取较高的密相区床层温度及较高
的床层厚度,以提高床层热容量。
5.5.4
在锅炉运行中过热汽温、再热汽温随着锅炉负荷、燃料性质、给水温度、炉膛锅炉空气系
数以及炉膛出口烟温等的变化而有较大的波动。喷水是为了在上述变化时保持汽温在规定的范
围(50%~150%设计值)内,并防止管壁超温。
为了保持汽温稳定,过热器、再热器采用辐射
式与对流式相结合的方式,见图5-28。由图5-28可
见,锅炉负荷变化时,对流过热器与辐射过热器的
汽温变化特性是相反的,对流过热器中,随着负荷
增加,蒸汽的焓增增大。这是由于在负荷增加时,
燃料消耗量增大,使烟气流速增加,而使烟气侧对
流放热系数增大;同时由于烟气温度增加,使传热
温差增大,因而使对流过热器吸热量增加的值超过
负荷增加值,从而使工质的焓增增加,因此锅炉负
荷增加时,对流过热器的出口汽温将要增加。在辐
射过热器中,则与此不同,随着锅炉负荷的增加,
虽然炉膛温度有所增加,循环流率也有所增加,但过热器的传热量跟不上蒸汽流量的增加,因
此使工质的焓增减小。因此,随锅炉负荷增加,辐射过热器的出口汽温是下降的。在设计过热
器时,如果同时采用辐射与对流过热器,并保持适当的吸热量比例,则可得到平稳的温度特性,
如图5-28中曲线3所示。
一般CFB锅炉设计时热量分配是这样确定的:先确定炉膛出口烟气温度和排烟温度。然
后确定空气预热器和省煤器吸热量。省煤器吸热量确定后就可确定炉膛水冷壁吸热量。去掉尾
部包墙受热面吸热量后,尾部剩下的就是对流过热器和对流再热器吸热量。炉膛中去掉水冷壁
吸热量后就是屏式过热器和屏式再热器吸热量。这样辐射和对流吸热量的分配以大致定下来
了。至于屏过和屏再的热量分配则按屏过升温80~100℃考虑,屏再的升温按100~120℃考虑。
根据几台100 MWe级CFB锅炉设计结果统计,屏式过热器的吸热量(焓增△i,kJ/kg)比例为
38%~42%,其中贫煤约为42%,烟煤约为40%,褐煤约为38%;屏式再热器吸热量比例为
50%~54%,其中贫煤约为54%,烟煤约为52%,褐煤为50%。
上述的分配比例已经包括了各级的喷水量热焓。为防止管壁超温应注意减小沿炉膛宽度方
向的水力和热力偏差。 5
-28
1.对流过热器 2.辐射过热器 3.总焓增 第五章 CFB锅炉主要性能参数及结构尺寸的计算及选择
162
在锅炉设计时必须预先估计到贫煤、无烟煤在分离器中可能的后燃现象,而采取相应的措
施,如减少过热器、再热器受热面积,否则运行时就要超温,而使喷水量过大。另外,汽机高
压缸排汽常比设计值偏高,造成再热器入口温度偏高,而使再热器喷水量过大。表5-13是几
台不同煤种的锅炉设计喷水比率(指喷水量占蒸汽流量的百分数)和喷水量。 5-13
(t/h)
过热器喷水 再热器喷水
贫煤锅炉
负荷
BMCR 75%THA 50 THA BMCR 75%THA 50 THA
喷水比率,%
4.15 6.62 8.19 1.54 0.23 0.44
二级喷水量和,t/h
18.21 19.0 15.9 5.47 0.533 0.72
烟煤锅炉
喷水比率,%
3.7 5.6 6.2 1.6 0.2 0
二级喷水量和,t/h
16.3 16.2 12 5.8 0.5 0
褐煤锅炉
喷水比率,%
2.85 5.77 4.78 1.22 0 0
二级喷水量和,t/h
12.52 16.7 9.0 4.39 0 0 从表
5-13看出,由贫煤炉到褐煤锅炉过热器喷水量有减小的趋势。再热器喷水量在低负
荷时应趋近于0。
5.5.5 sSO2CSO2
脱硫效率与给定的SO2排放浓度
CSO2,燃料中硫的含量Sar及干烟气体积Vgy有关,见式
(5-60)。
当褐煤含硫量Sar>1.5%
,其他煤种含硫量>3.0%和要求排放浓度≤400 mg/m3(标态)时,按
式(5-60)计算,要求的脱硫效率均要大于94%。
对于要求如此高的脱硫效率,除选择活性好的石灰石,并还应增加脱硫剂在炉内的停留时
间和保证最佳的炉膛脱硫的反应温度。
氧化氮的排放浓度CNox从已做考核试验的锅炉来看,均能达到设计值,小于
400 mg/m3(标
态,O2=6%)
。 5.6 1) 根据燃料的元素分析及过剩空气系数α进行温焓表计算,求出理论空气量V0和烟
气体积Vy。
2) 根据锅炉设计规范(锅炉蒸发量及蒸汽参数等)、燃料发热量Qnet,ar进行热平衡计
算,求出锅炉计算煤耗量Bj。
3) 给定飞灰份额afh、分离器效率fl进行循环流率
Gs、物料携带率Mwl、炉出口物料
浓度Cp及炉膛内物料浓度分布的计算,炉内物料浓度分布也可通过沿炉膛高度的
压力分布来计算。 第五章 CFB锅炉主要性能参数及结构尺寸的计算及选择
163
4)
进行炉内受热面的布置,包括双面水冷壁、过热器屏、再热器屏以及耐火耐磨材
料涂层等。
5) 根据给定的床侧温度和炉内平均物料浓度等参数进行炉内传热计算,求出炉内各
受热面的传热系数及传热量,确定受热面积,并进行校核。
6) 给定一次风率r1和炉膛密相区空截面风速
Wm,求出布风板截面积。
7) 给定炉膛稀相区空截面烟气速度Wx,求出炉膛横截面积。
8) 根据给定的炉膛出口温度,通过炉内传热计算,可求出炉膛的高度,此高度还应
进行燃料燃尽度的校核(一般以烟气在炉内的停留时间来表征)。
9) 进行二次风口、给煤口、石灰石给料口、排渣口布置及有关尺寸的确定。
10) 不同容量锅炉性能设计参数的相互借鉴。
对于130 t/h到670 t/h容量CFB锅炉,当锅炉结构型式相同,煤质相同或相近,分离器型
式相同时,其设计性能参数和运行经验均可以相互借鉴,只是容量增大后:
(1) 二次风速要适当提高,以增加穿透能力;
(2) 给煤点要适当增加,以达到给煤均匀性;
(3) 必要时床层厚度可适当增加以及由此而引起的床压增加、密相区风速增加等。对增加
床层厚度所带来的利弊要综合分析后再做决定。
(4) 在煤质条件相同和炉膛空截面速度相同的情况下,大炉子的高度可能增大,因而停留
时间增长。燃尽效率和脱硫效率提高。
实际上炉膛的设计远比上述讨论的要复杂,在每一步中还要用到其他方面的一些知识,如
流动、燃烧、传热等。有些时候还要根据运行经验来修正。
部分主要性能设计参数、尺寸确定顺序及影响关系见图5-29。一些100~150MWe级CFB
锅炉主要性能参数选择范围见表5-14,表中数据为根据2005年普华中心CFB锅炉专家研讨会
讨论结果整理编写。 第五章 CFB锅炉主要性能参数及结构尺寸的计算及选择
164
5
-29 第五章 CFB锅炉主要性能参数及结构尺寸的计算及选择
165
5-14 (100~150)MWeCFB()
锅炉燃用
煤种
入炉粒度级配①
一次
风率
r1(
%)
密相区
风速
Wm(m/s)
稀相区
烟速
Wx(m/s)
停留
时间
τ(s)
炉膛出
口温度
T(℃)
床温
下限
(℃②)
飞灰
分额③ fh(
%)
飞灰/炉渣
可燃物
Cfh/Clz
q4
(%)
锅炉
效率 k(
%)
最低稳燃
负荷
率%BMC
R
SO2
排放量④
(mg/Nm3)
NOx
排放量
(mg/Nm3)
dmax
mm
d50
mm
d<0.2mm
份额%
石油焦
8~10 1~1.2
15
(不可控)
50~55 ~4 4.6~4.8 6~7
860
~900
>800 50~55 15~18 / 2 4.5~6.0 88~89 40~45 400~800 <400
Vdaf≤
5%
无烟煤
4-5 0.5~0.7 <10~20 50~55 ~4 4.8~5.0 6~7
920
~950
>800 40~50 18~20 / 2 4.7~6.0 86~88 45~50 200~400 <150
Vdaf>
5%
无烟煤
5-6 0.6~0.7 <10~20 50~55 ~4 4.8~5.0 6~7
900
~920
~800 40~50 14~16 / 2 4.0~4.5 86~89 40~45 200~400 <150
Vdaf≤
15%
贫煤
6~7 0.7~1.0 <10~20 50~55 4~4.5 5.0~5.2 6~7
880
~900
~760 50~55 12~14 / 2 3.5~4.0 89~90 35~40 200~400 <200
Vdaf>
15%
贫煤
7~8 1.0~1.2 <10~20 50~55 4~4.5 5.0~5.2 6~7
880
~900
~750 45~55 10~12 / 2 3.0~3.5 89~90 30~35 200~400 <250
Vdaf≤
30%
烟煤
6~8 0.8~1.0 <10~20 ~50 ~4.5 5.0~5.5 6.0~6.5
870
~880
~730 50~60 6~8 / 1.0 2.5~3.0 90~90.5 30 200~400 <250
Vdaf>
30%
烟煤
8~10 1.0~1.5 <10~20 ~50 ~4.5 5.0~5.5 6.0~6.5
870
~880
~730 45~55 5 / 1 1.5~2.5 90~91.5 30 200~400 <250
褐 煤
8~12
1.2~1.8
8~10 ~45 4.0~4.5 5.0~5.5 6.0~6.5
850
~870
~650 60~70 3 / 0.5 0.6~1.5 89~90 30 200~400 <300
油页岩
8~10 0.8~1.4 <10~20 50~55 4.0~4.5 5.0~5.5 6.0~6.5
880
~890
~730 40~45 4/ 1 5~7 84~86 40 <400 <300
矸 石
5~7 0.8~1.2 <15~20 ~50 4.0~4.5 4.8~5.2 6.0~6.5
880
~890
~730 45~50 6 / 2 5~7 86~88 40 200~400 <250
煤 泥
3~5
0.5~0.7
5
~50 3.5~4.0 5.0 6.0~6.5
870
~890
~720 60~65 8 / 1 2.0~3.0 88~89 40~45 200~400 <250
注: ①用线算图表示的入炉煤粒度分布见图5-19~5-27;②指不投油最低稳燃负荷下最低床温;③当燃料中Aar%
含量太高时(Aar>35%)不利于燃烧,底渣份额增多,因此
第五章 CFB锅炉主要性能参数及结构尺寸的计算及选择
166
煤的粒度级配dmax 和
d50选用低限,飞灰份额afh% 也选用低限;④投石灰石条件下;⑤本表根据谱华中心CFB锅炉专家研讨会讨论结果修订。
第五章 CFB锅炉主要性能参数及结构尺寸的计算及选择
百度云下载:链接:https://pan.baidu.com/s/1D_wr7yKgwkZJ1keoEqYCRw
提取码:orga
锅炉的性能和结构图解(底部 PDF下载)
导读:如前所述,循环流化床锅炉燃烧室中上部为快速床。固体物料在一定气速条件下流化,当
气速低于Uc时,固体循环量对床层空隙率无明显影响;气速一旦超过
Uc,床层空隙率主要取
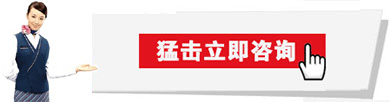